
El 16 de noviembre de 2017 se entregó en Frankfurt por cuarta vez consecutiva el premio de diseño en impresión 3D del purmundus challenge durante la feria formnext. Un total de cinco proyectos obtuvieron el desado trofeo dorado.
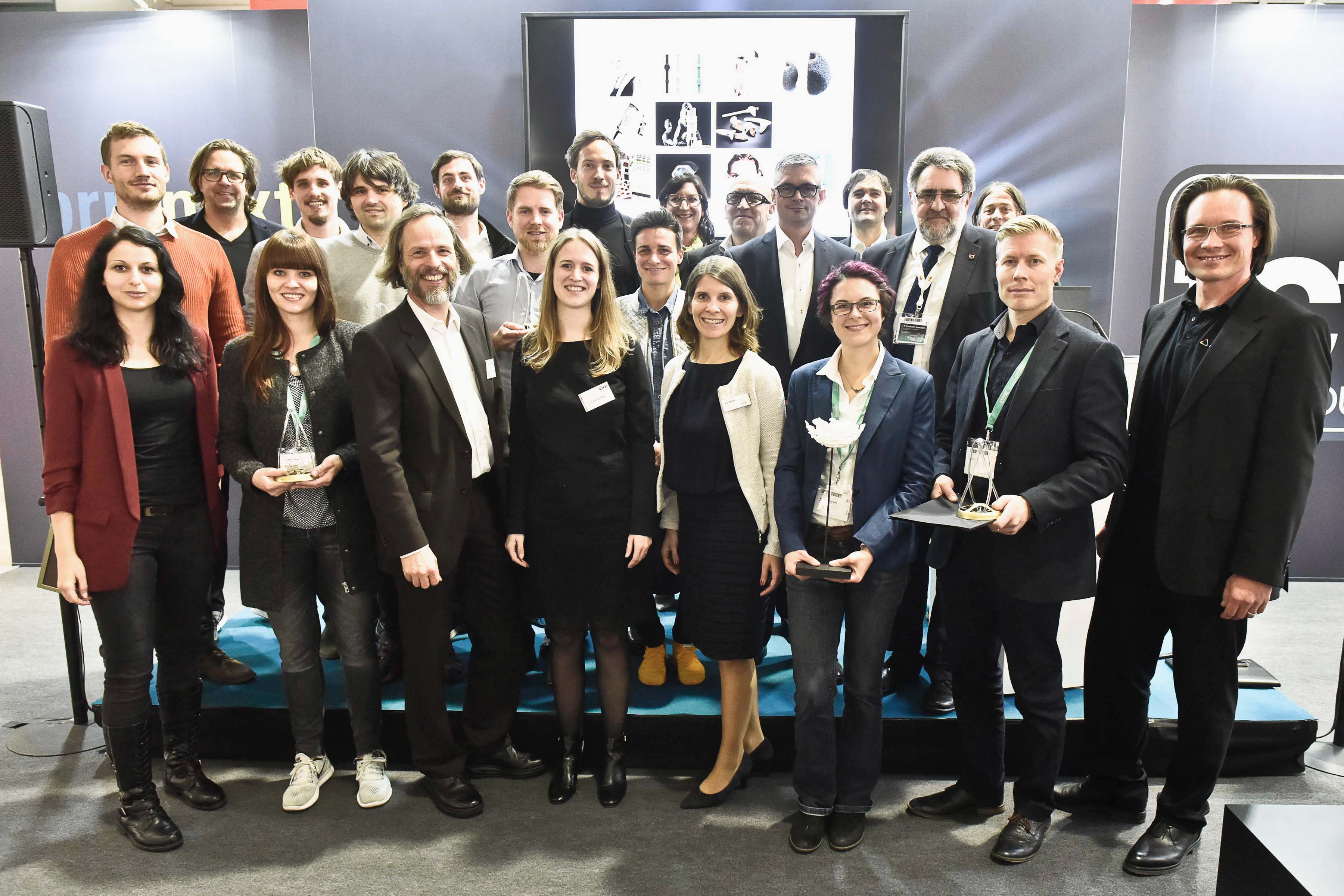
Hoy en día las posibilidades de la fabricación aditiva son tan amplias como no lo habían sido nunca en las últimas tres décadas. Hoy en día existe una gran variedad en la elección de las características de los materiales, así como en los métodos de fabricación en la adición capa por capa. Finalmente se han podido combinar las tecnologías convencionales con las aditivas. La concepción meditada de un buen prototipo puede lograr que este desarrolle todo su potencial y tenga un encanto especial si se hace una elección y combinación correcta de los materiales y las tecnologías.
¿Por qué no combinar de manera inteligente la variedad de posibilidades de diseño que ofrece la producción aditiva?
Bajo el lema „Fusión – combinación inteligente de impresión 3D“, 45 finalistas de todo el mundo presentaron los diseños más destacados entre el catorce y el diecisiete de noviembre del 2017 en la feria formnext. Un jurado internacional entregó en Frankfurt los galardones por valor de 12.000 € a un total de seis ganadores. Este se entregó por primera vez el „Premio de Innovación“ a visiones progresistas, es decir, a proyectos que demostraron cómo la impresión 3D puede cambiar el mundo de la fabricación de productos.
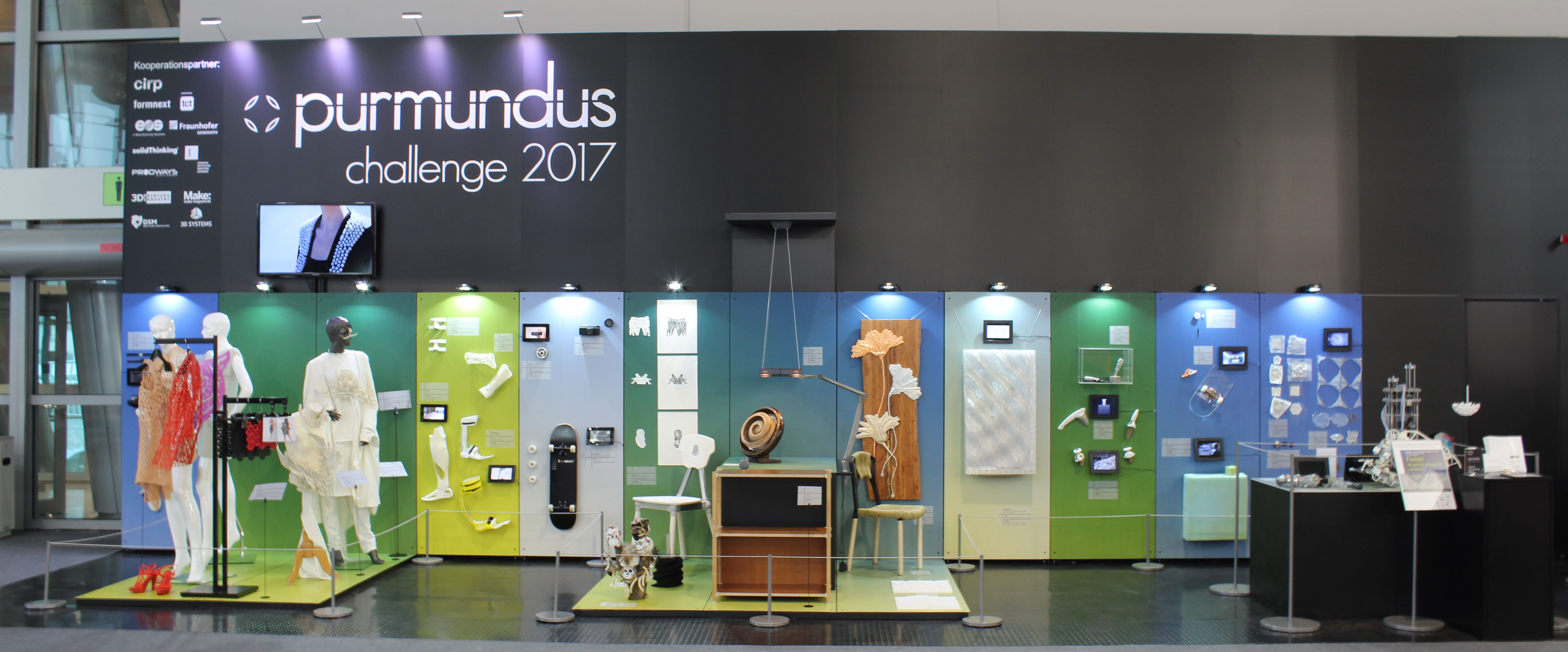
Los ganadores de este año son:
1. Premio: Nacimiento de Venus
Danit Peleg 3D I Danit Peleg

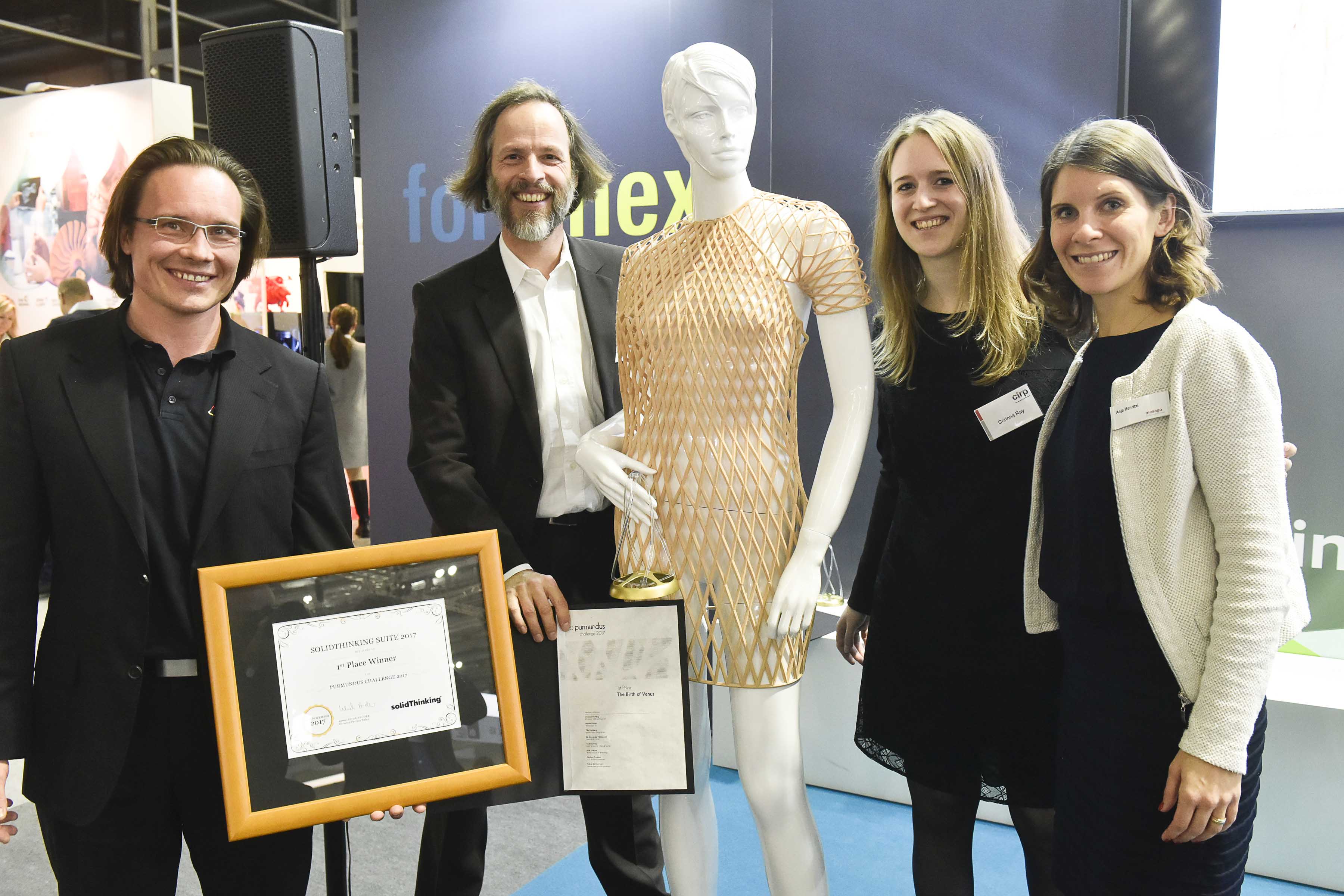
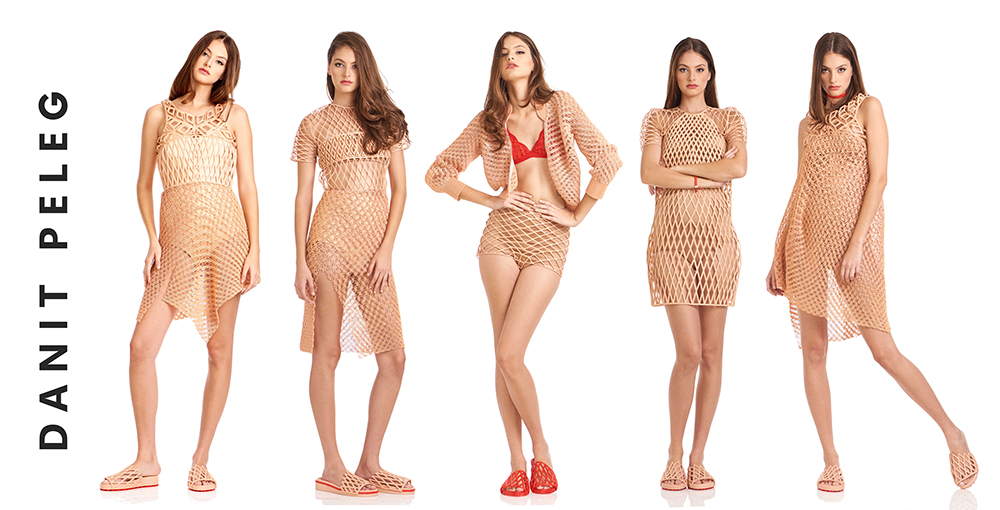
2. Premio: Morfología fluída
Universidad Técnica de Múnich, Cátedra de Proyección y Cubiertas de Edificios I Moritz Mungenast I Oliver Tessin I Viktoria Blum I Tobias Gutheil I Olga Khuraskina I Luc Morroni

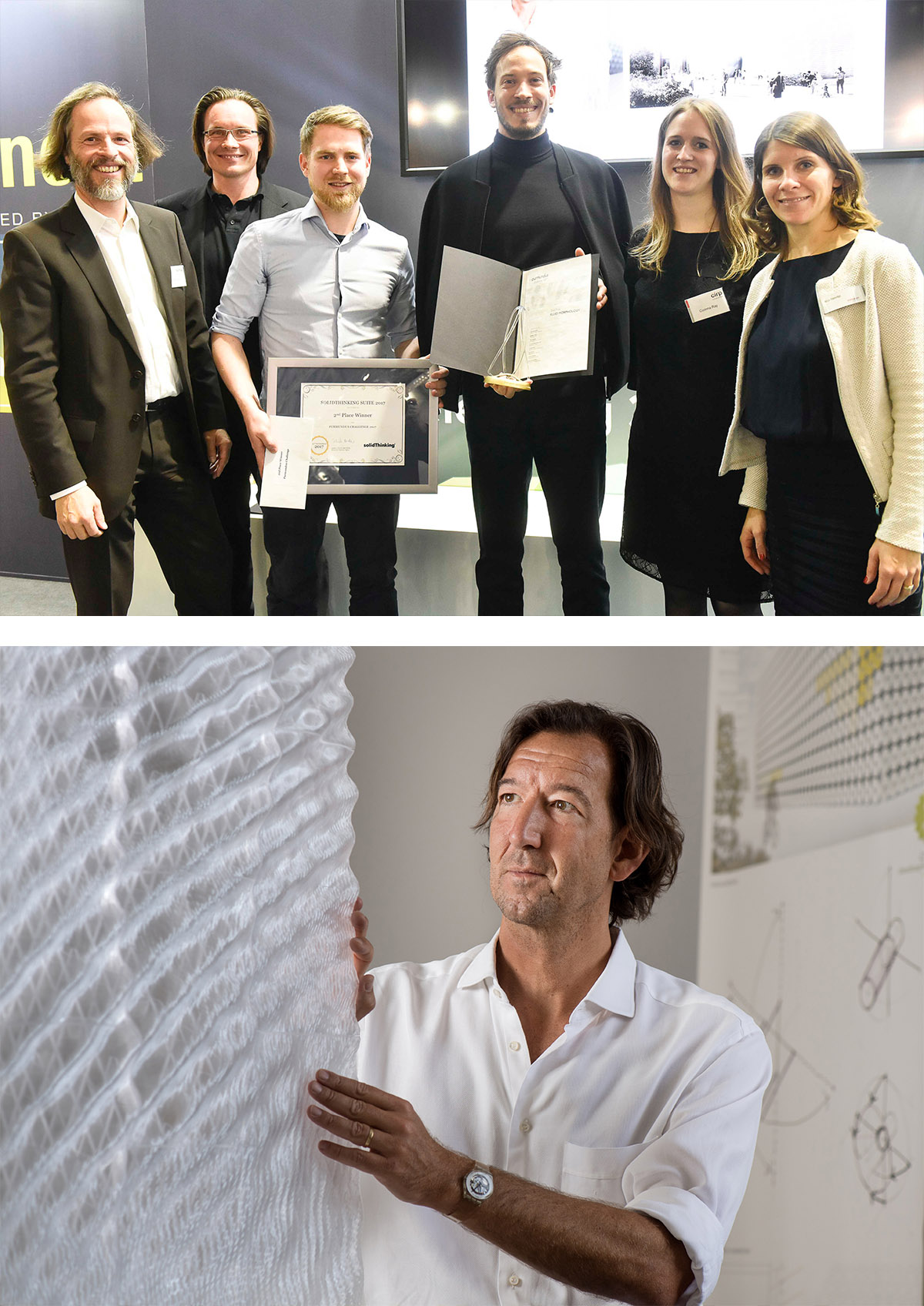
Mortiz Mungenast, investigador de la Cátedra de Proyección y Cubiertas de Edificios de la Facultad de Arquitectura en la Universidad Técnica de Múnich, ha sido el responsable de iniciar y dirigir este proyecto.
MORFOLOGÍA FLUÍDA es el primer elemento de fachada translúcido y multifuncional que se fabrica con un solo proceso de impresión 3D. Este proyecto de investigación refleja el potencial de la impresión 3D dentro del sector de la construcción y de las cubiertas de edificios. Puesto que además todas las etapas se enmarcan en el proceso digital (el diseño, la planificación, y la producción) consigue con ello cerrar la cadena digital. Otro aspecto innovador es la integración de funciones de un material en un elemento constructivo: MORFOLOGÍA FLUÍDA incluye funciones de la fachada como la distribución del peso, el aislamiento, la opacidad, el uso de la luz, la ventilación o la difusión de los ruidos.
Además de la búsqueda de nuevas posibilidades para solucionar los futuros desafíos a nivel global dentro del sector de la construcción, como son por ejemplo los nuevos materiales de construcción y el ahorro energético, el objetivo de MORFOLOGÍA FLUÍDA es reducir la tecnología en los edificios, establecer un círculo cerrado de materiales y facilitar el proceso de construcción a través del uso sensato de las herramientas digitales.
También han participado en este proyecto Oliver Tessin, asistente de proyectos, y Viktoria Blum, Olga Khuraskina, Luc Morroni y Tobias Gutheil, estudiantes del Máster de la Universidad Técnica de Múnich. La Cátedra de Proyección y Cubiertas de Edificios es miembro del Laboratorio de Investigación de la Facultad de Arquitectura y del Grupo TUM – Manofactura Aditiva para la Construcción. Proyecto financiado por Rodeca, Picc`s 3D World y Delta Tower.
3. Premio: OTP Grasshopper
Mecuris GmbH I Manuel Opitz I Clemens Rieth I Benjamin Els

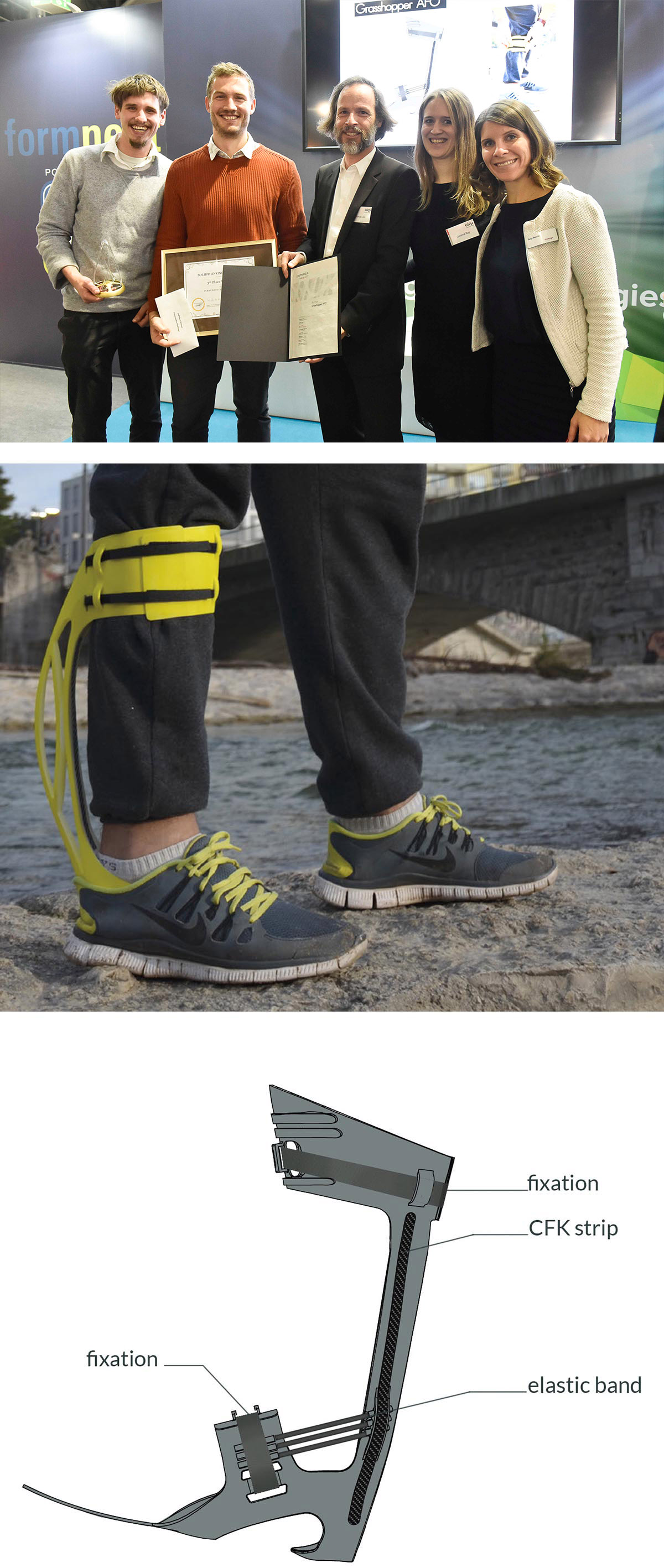
Actualmente, las OTP que se encuentran disponibles con mayor frecuencia en el mercado son las OTP termoplásticas hechas a medida del paciente y las prefabricadas en fibra de carbono. Las OTP termoplásticas imitan la anatomía de cada paciente permitiendo una adaptación más cómoda. Sin embargo, el proceso de fabricación de este tipo de OTP es largo y requiere un mínimo de tres semanas para cada ortesis. El material de las OTP de fibra de carbono ofrece mejores propiedades, como por ejemplo la fuerza o el retorno de energía. Este tipo de OTP se fabrica en serie y no se adapta a las necesidades individuales de cada paciente.
La OTP Grasshopper tiene como objetivo combinar la cualidad de adaptación a cada paciente de las OTP termoplásticas con las propiedades de alta calidad del material de las OTP de fibra de carbono. Esto es posible gracias a la utilización de tecnologías como el escáner 3D, el diseño asistido por ordenador (CAD) y la fabricación aditiva (impresión 3D). La fibra de carbono se aplica como una banda sobre el dispositivo y con ayuda de una herramienta manual se funde con la OTP. Actualmente el proceso completo de fabricación desde el registro de datos hasta el envío de la OTP dura 10 días laborables.
Gracias a la automatización del software y a la diversidad que ofrece la impresión en 3D es posible fabricar la OTP Grasshopper en un corto periodo de tiempo. El escáner de la pierna del paciente se guarda en una plataforma en línea junto con determinados parámetros técnicos. Esta información se usa posteriormente para crear de manera automática una OTP que se adapte a las necesidades específicas de cada paciente. Esto es una dato relevante en el caso de niños ya que crecen muy rápido. La capacidad de adaptación de la OTP significa que esta se va a poder usar también con pacientes que tengan una gran deformidad. El hecho de aplicar la fibra de carbono con un dispositivo manual permite a los técnicos ortopédicos y a los médicos seguir adaptando las OTP y, si fuera necesario, añadir un soporte extra.
Mención especial: Algas dinámicas
Dorothea Lang

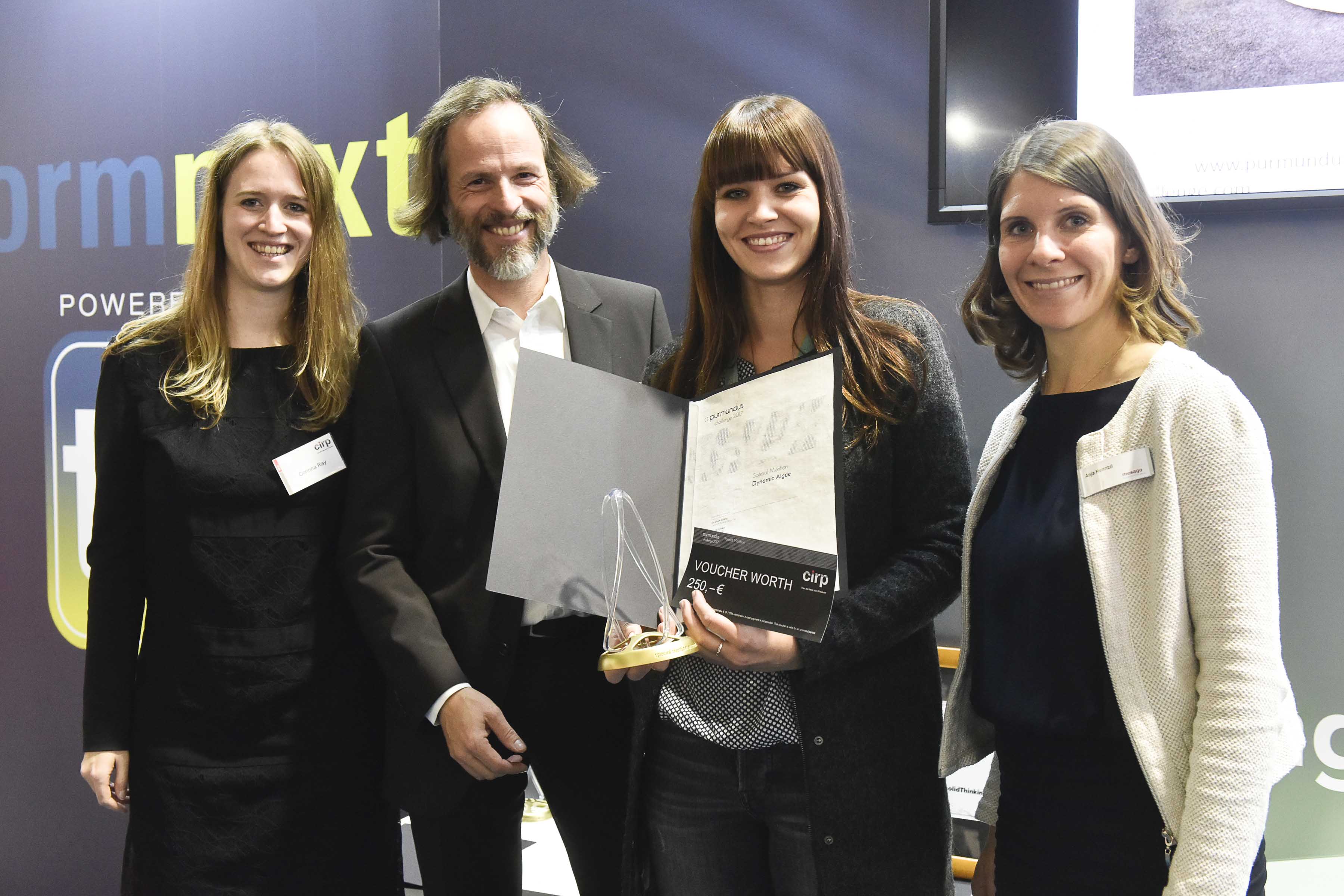

Premio de Innovación: Impresión InFoam
Dorothee Clasen I Sascha Praet I Adam Pajonk

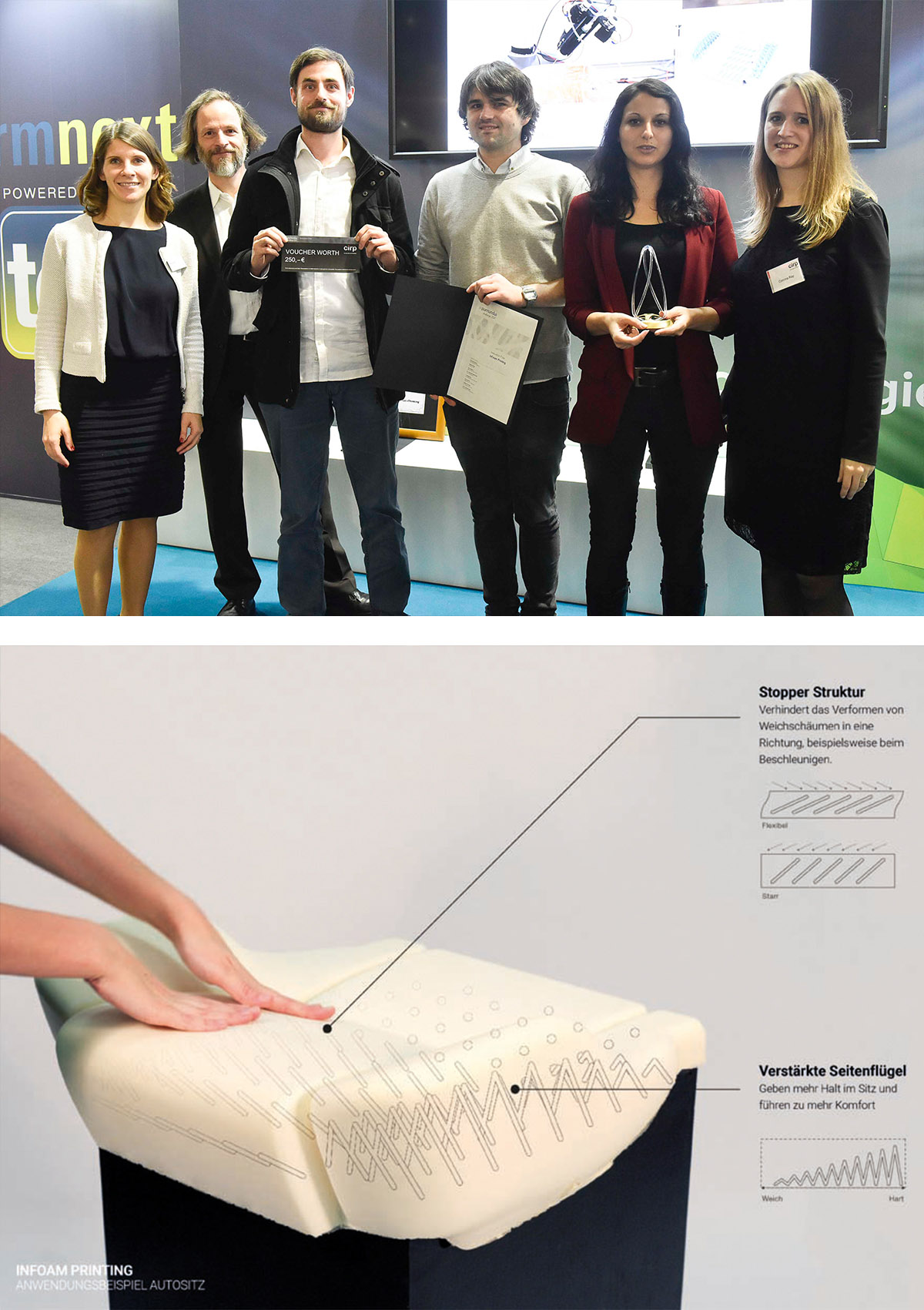
El proceso de impresión InFoam simplifica considerablemente el proceso de fabricación de las piezas de espuma, así como el proceso tedioso de inyección de elementos integrados en la espuma. Además, también permite que los elementos se solidifiquen sin sujección dentro de la espuma. Esta tecnología abre un abanico de posibilidades permitiendo que el material que se inyecta en la espuma se pueda personalizar y adaptar su grado de dureza de manera gradual. Gracias a las estructuras integradas se pueden conseguir efectos cinéticos novedosos en las piezas de espuma cuya función se puede emplear particularmente en el diseño de productos. De esta manera se podría programar, por ejemplo, un cubo de espuma con un movimiento de torsión que a su vez se pueda usar con fines ergonómicos como asiento acolchado o protector ortopédico. El hecho de poder integrar una estructura similiar a los muelles podría revolucionar el mercado en el sector de colchones.
El ámbito de aplicación de la impresión InFoam es amplio debido al número de productos que contienen espumas: colchones, muebles tapizados, plantillas ortopédicas o incluso también asientos de coche. Los elementos de espuma no solo son personalizables, sino que además tienen características completamente nuevas gracias a las estructuras integradas. De esta manera, los asientos de coche podrían contrarestar la fuerza de determinadas estructuras y su vez ofrecer una sujección especial en caso de accidente. También se podrían mejorar los colchones para cada persona de manera individual adaptándolos con un escáner 3D corresondiente. La impresión InFoam permite en principio reforzar la espuma sin tener que cortarla, pegarla o fundirla.
La idea de la tecnología InFoam surgió en un taller de 5 días organizado por Covestro en la Universidad Técnica de Münster en el que participaron dieseñadores y arquitectos.
Premio del público: Ultimate grip - Empuñadura personalizada para cuchillos
Go3D Ltd I Antti Korpi
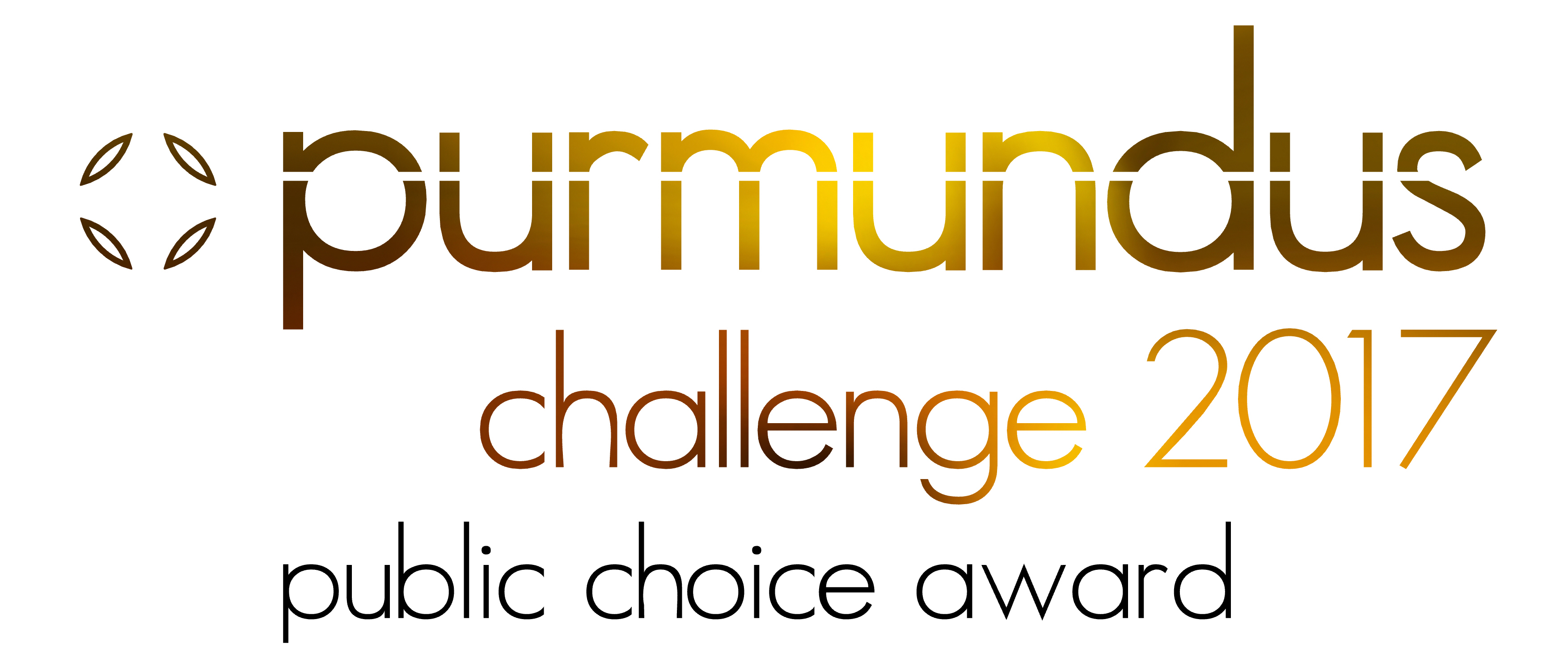
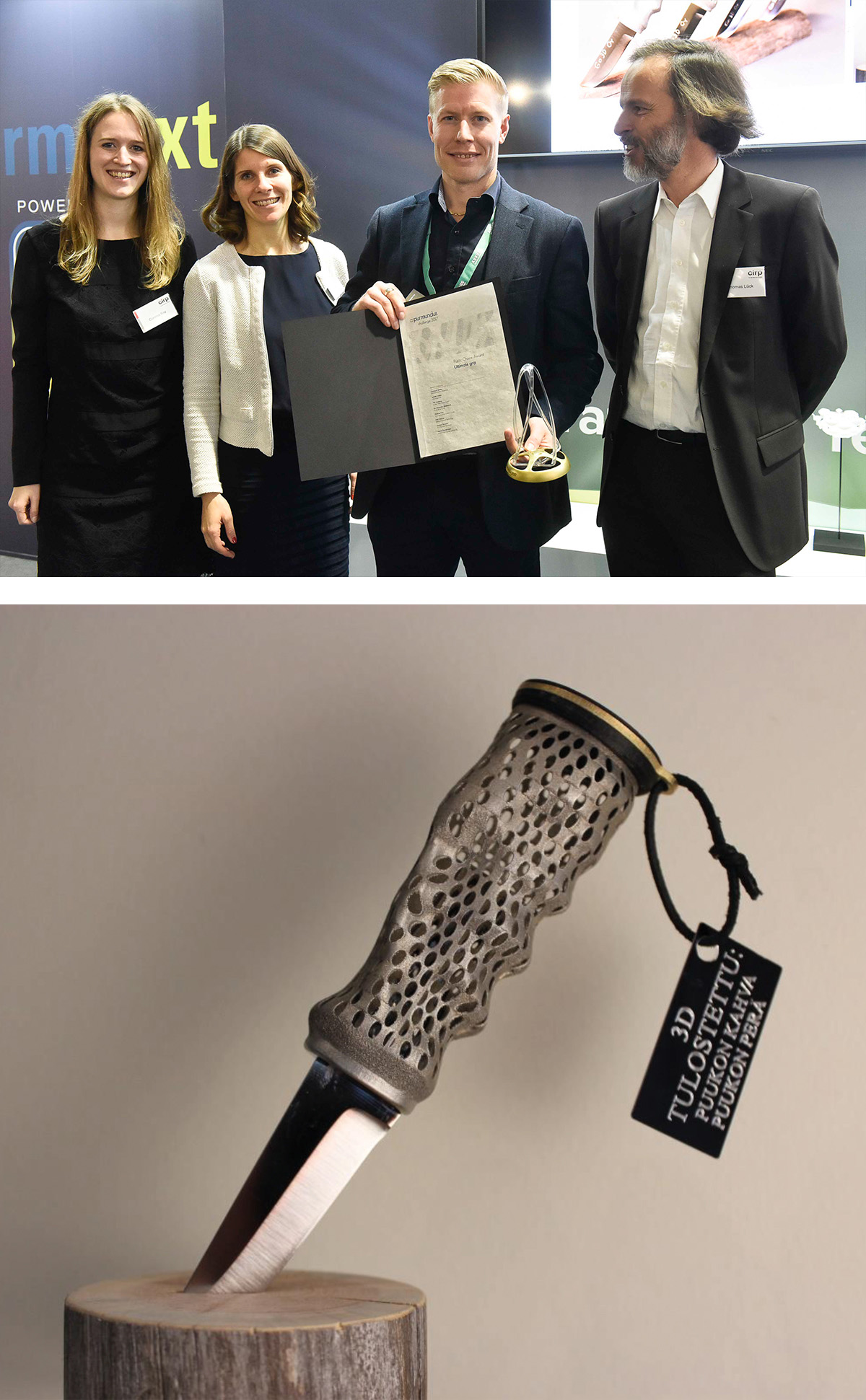
El producto Ultimate Grip es la combianción de un mango creado con las tecnologías más innovadoras y una hoja cuyo proceso de fabricación se usa desde el siglo pasado. El diseño y el desarrollo del producto se basan en las siguientes pautas:
- diseño sin soportes
- las piezas se imprimen directamente en un panel de construcción
- se retira la pieza mediante serrado
- apenas se necesita procesar las piezas con posterioridad
- se puede apilar y tiene una orientación óptima de impesión. Proceso completo en sala
- Montaje mecánico sin herramientas especiales, pegamento, remaches, etc
- Optimización topológica
1. 1. Empuñadura personalizada. La empuñadura se fabrica en función de la huella palmar del usuario.
- a. mejora el agarre, la seguridad y la ergonomía
- b. la orientación de la muestra se puede elegir como se desee
- c. una vez se tenga la huella palmar, se pueden realizar distintos diseños adaptados a la persona para la que se realice el encargo
- a. Ligero
- b. diseño exclusivo
- c. resistencia mínima (uso bajo el agua)
- d. diseño con forma de red que mejora el agarre
- e. reducción del material: se necesita menos energía para el calentamiento de la empuñadura
Una buena ergonomía, la seguridad y un diseño exclusivo son en definitiva características interesantes para futuros clientes, usuarios finales y también para aquellas empresas que hagan uso de los cuchillos de manera profesional.
Los finalistas de este año (FOTOS):












































×
!Desde aquí nos gustaría dar las gracias al jurado y a los colaboradores!
Jurado 2017
Christoph Behling - Christoph Behling Design Ltd.Isabelle Fröhlich - Volkswagen AG Tilla Goldberg - Ippolito Fleitz Group GmbH Dr. Alexander Hildebrandt - Festo AG & Co. KG Andreas Pany - Ernst Strassacker GmbH & Co. KG Prof. Dali Sun - Beijing University of Technology Graham Tromans - G. P. Tromans Associates Rainer Zimmermann - zimmermann produktgestaltung