
El 11 de noviembre de 2020 tendrá lugar la octava entrega de los premios de diseño en 3D y 4D del purmundus challenge durante la celebración de la feria digital Formnext Connect. El concurso se retransmitió en directo y sorprendió con una nueva categoría de premios y nuevos colaboradores. Un total de siete propuestas obtuvieron el codiciado trofeo dorado.
El purmundus challenge 2020 ha demostrado la resistencia a la crisis de la fabricación aditiva. “En un año lleno de retos como ha sido el 2020, se ha puesto de nuevo de manifiesto la relevancia de la impresión 3D y 4D. La comunidad en torno a la fabricación aditiva ha realizado un esfuerzo conjunto y ha logrado explorar nuevos caminos no solo en lo referente al valor añadido de carácter social, sino también en lo que ha diseño se refiere”, comenta Dennis Lang, responsable de Comunicación y Relaciones Públicas del purmundus challenge. Los ganadores destacan por la amplia variedad de los sectores a los que pertenecen. Todos ellos han aportado su visión particular a la interpretación del lema de este año “Geometría y material en harmonía”. “Las aplicaciones de la fabricación aditiva que persiguen un ideal, sobre todo aquellos beneficiosos para el medio ambiente, tienen una muy buena acogida”, añade James Helliwell, de la empresa hyperTunnel Limited y jurado del purmundus challenge. Mientras tanto, empresas, institutos, universidades, estudios de diseño y empresas de nueva creación emplean la impresión 3D y 4D como medio para transgredir los ámbitos de aplicación hasta ahora conocidos y hacen uso intensivo de las técnicas de posprocesamiento.
Un total de 35 finalistas expondrán sus excelentes diseños de manera virtual del 10 de noviembre al 31 de diciembre de 2020 en la fería líder del sector Formnext Connect. La plataforma digital permite echar un vistazo fascinante en el mundo de la impresión 3D y 4D, y además, por primera vez, ofrece la oportunidad de ponerse en contacto con los propios diseñadores con ayuda de la función Matchmaking.
Los ganadores de este año son:
1. Premio: Moorhuhn Fahrradrahmen
HUHN cycles I Ralf Holleis

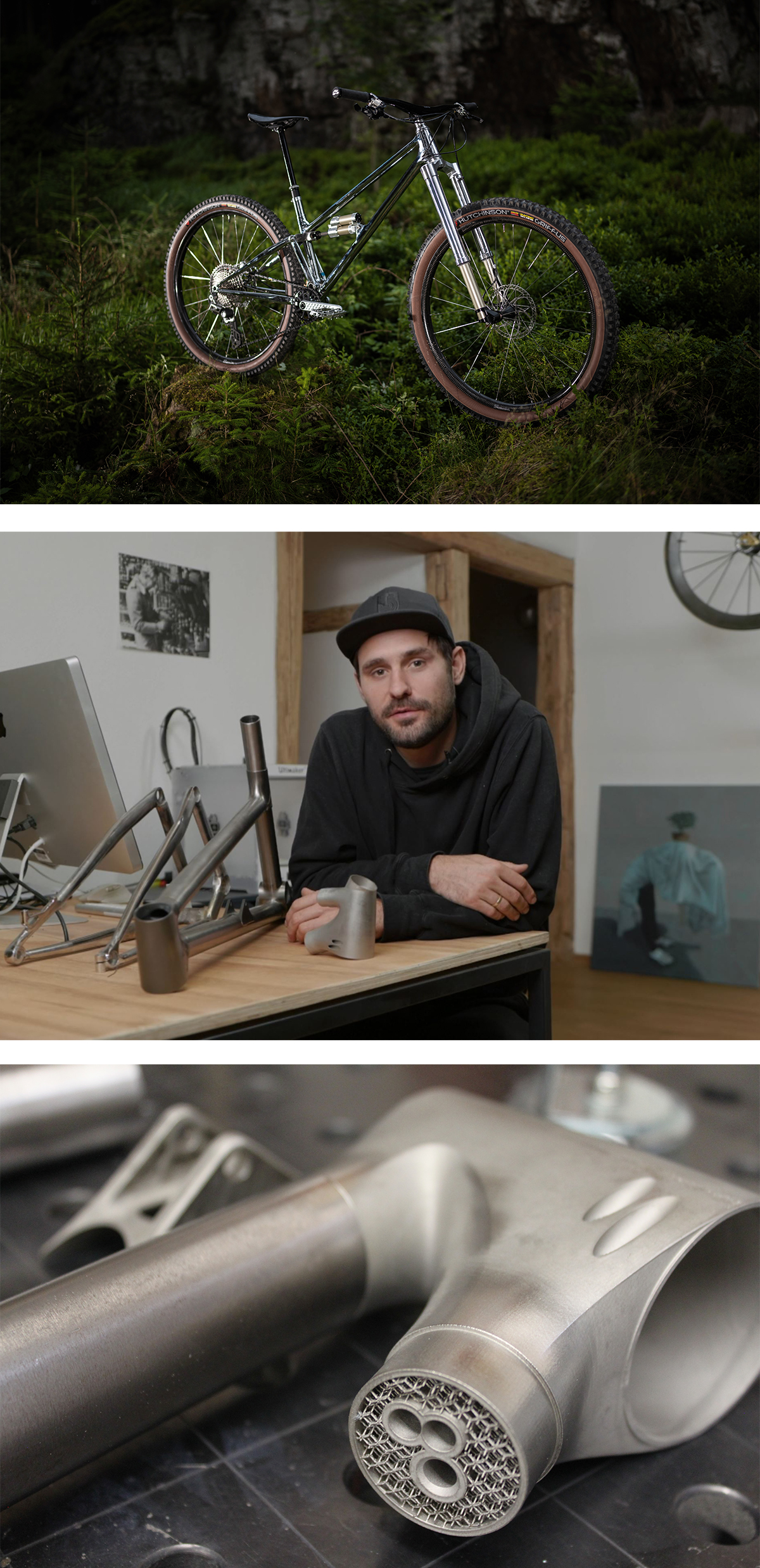
El titanio es un material que podría competir con las ventajas de la fibra de carbono ofrece para la construcción de marcos de bicicleta. Sin embargo, su procesamiento es complejo y por lo tanto el diseño es limitado. Desde el punto de vista de la funcionalidad, los cuadros de titanio dan la sensación de ser más suaves que los de carbono debido a las uniones soldadas de los tubos.
La Moorhuhn combina las ventajas de los tubos de titanio ultra ligeros y los conecta usando lengüetas producidas con fabricación aditiva; lo que hace que las uniones sean realmente sólidas pues se pueden diseñar en función de las fuerzas del cuadro de la bicicleata y distribuirlas de manera ecuánime. Las uniones son tan ligeras cómo sólidas gracias a una estructura reticular interior que sirve de apoyo para las finas paredes. Además, la fabricación aditiva hace posible producir cada marco de bicicleta en función de las necesidades de cada individuo, puesto que no se requiere de ninguna herramienta. Se pueden integrar en el diseño funciones como la guía de cableado, las bridas del sillín, las carcasas de los cojinetes o material adicional para la soldadura, lo cual facilita enormemente la labor de los constructores de cuadros.
Estos son muchos detalles friquis, así que resumiendo en pocas palabras: la fabricación aditiva hace posible construir modernas bicicletas de montaña de titanio que son tan ligeras y rígidas como los marcos de fibra de carbono, pero la fabricación es local y personalizada para cada ciclista. Lo más importante es que el proceso de producción es mucho más respetuoso con el medio ambiente y los marcos se pueden tanto reparar como reciclar. No tiene sentido tirar al vertedero una bicicleta de montaña moderna tras dos años porque no sea seguro repararla. Los cuadros de titanio no necesitan pintura puesto que no se corroen, por lo que el acabado no requiere el uso de químicos que pongan en riesgo la salud del fabricante.
2. Premio: exomotion® hand one
HKK Bionics GmbH I Dominik Hepp

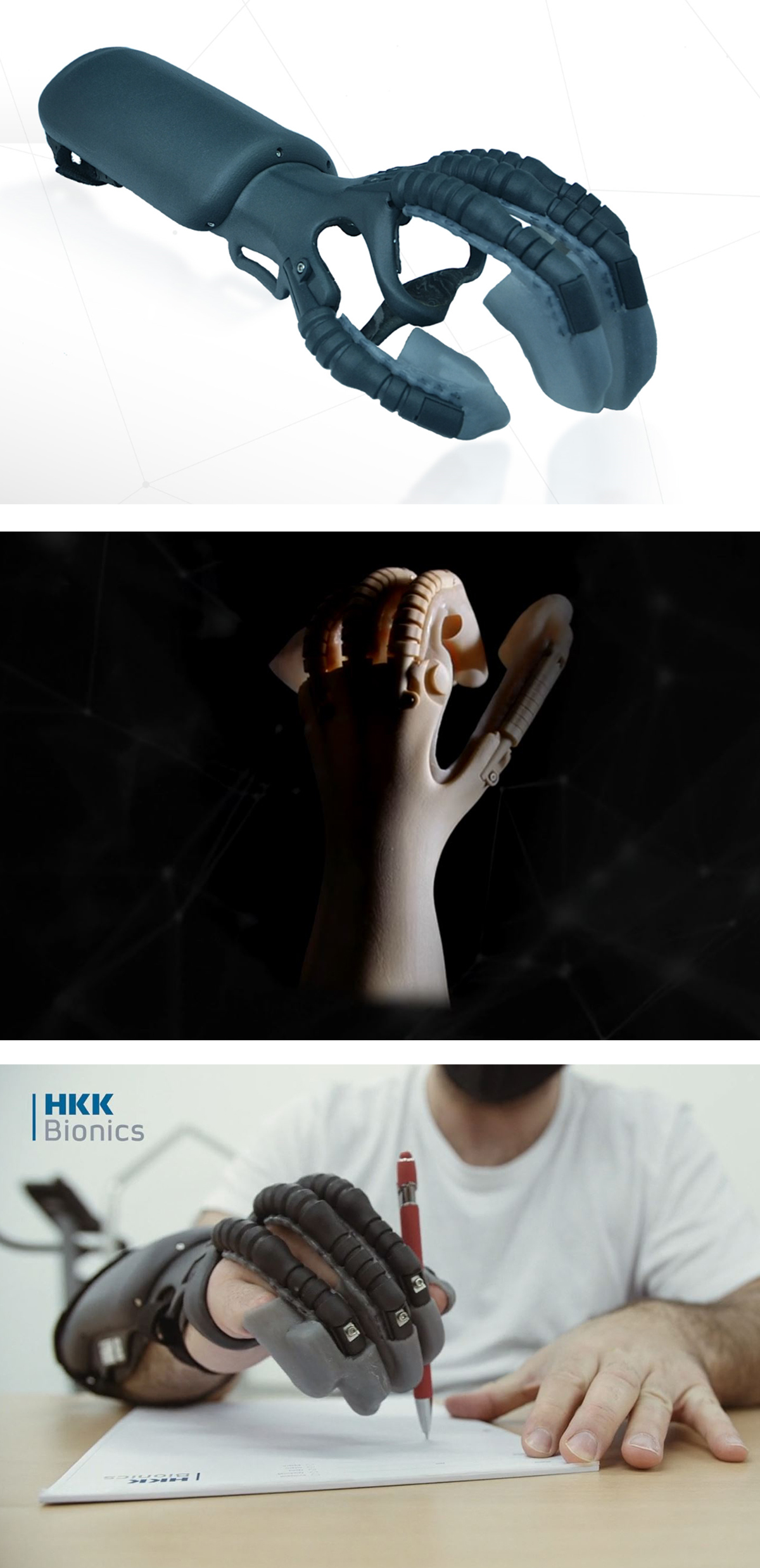
El principio functional: un software inteligente con un sensor asociado reconoce la intención de movimiento del portador a través de un músculo que todavía está activo controlando potentes micro dispositivos situados en la férula del brazo. Estos micro dispositivos transmiten energía a los mecanismos de actuación del guante, los cuales abren y cierran los dedos haciendo que tengan la fuerza de agarre necesaria. Todos los componentes están conectados por la férula de apoyo del brazo, la cual se personaliza para cada paciente.
Estos son los elementos que junto con una unidad de control para un uso sencillo e intuitivo, y una batería potente conforman la exomotion® hand one. Es un recurso cotidiano de larga duración que cubre una brecha de mercado. La órteis de mano puede ejecutar seis tipos distintos de agarre, como el agarre de fuerza o de pinza que abarcan las aplicaciones más relevantes. Las variables predefinidas determinan cuáles son los dedos involucrados en el agarre para crear un agarre que sea lo más funcional posible. Es necesario recurrir a la fabricación individualizada para garantizar que todas las órtesis se adapten a la perfección y se puedan usar a diario sin hacer heridas. HKK Bionics GmbH trabaja con tiendas de suministro médico con formación previa. Esta cooperación combina el procesamiento manual de siliconas médicas con el escáner 3D, la construcción automatizada y el sinterizado láser. Se ha desarrollado un sistema modular para poder fabricar para cada paciente un producto técnico de manera económica, que incluye piezas estándar así como una férula individualizada para el brazo y con una fabricación parcialmente automática que lleva a cabo un proveedor profesional de servicios de impresión 3D. A su vez, la fabricación aditiva permite integrar secciones para componentes, componentes mecatrónicos y crear huecos. Se puede alcanzar un nivel de miniaturización que no está al alcance de los medios de producción convencionales. Mientras que la longitud y el peso disminuyen, aumenta la aceptación de la órtesis por parte del paciente.
Todas las partes plásticas de la ortésis están impresas mediante sinterización láser con material PA12 biocompatible en el color que el paciente desee. El proceso individualizado de construcción y la coloración hacen que cada prótesis sea única. También es posible customizar la superficie. Estas técnicas de acabado y coloración para la impresión, disponibles desde hace tan solo unos años, han hecho posible fabricar productos como la exomotion® hand one, que tienen un acabado de alta calidad compatible con los dispositivos médicos. Para la fabricación de la férula del brazo, que se basa en el escáner 3D de un modelo de escayola del brazo del paciente, se desarrolló un software de construcción parcialmente automatizada con el que se pudo reducir el tiempo de construcción de este tipo de geometrías complejas e individualizadas a tan solo un par de horas y que ,a su vez, cumplía con los requisitos de reproducibilidad de los dispositivos médicos.
3. Premio: ZERO - 3D printed sneakers
Svet Abjo I Zellerfeld Shoe Company Inc.

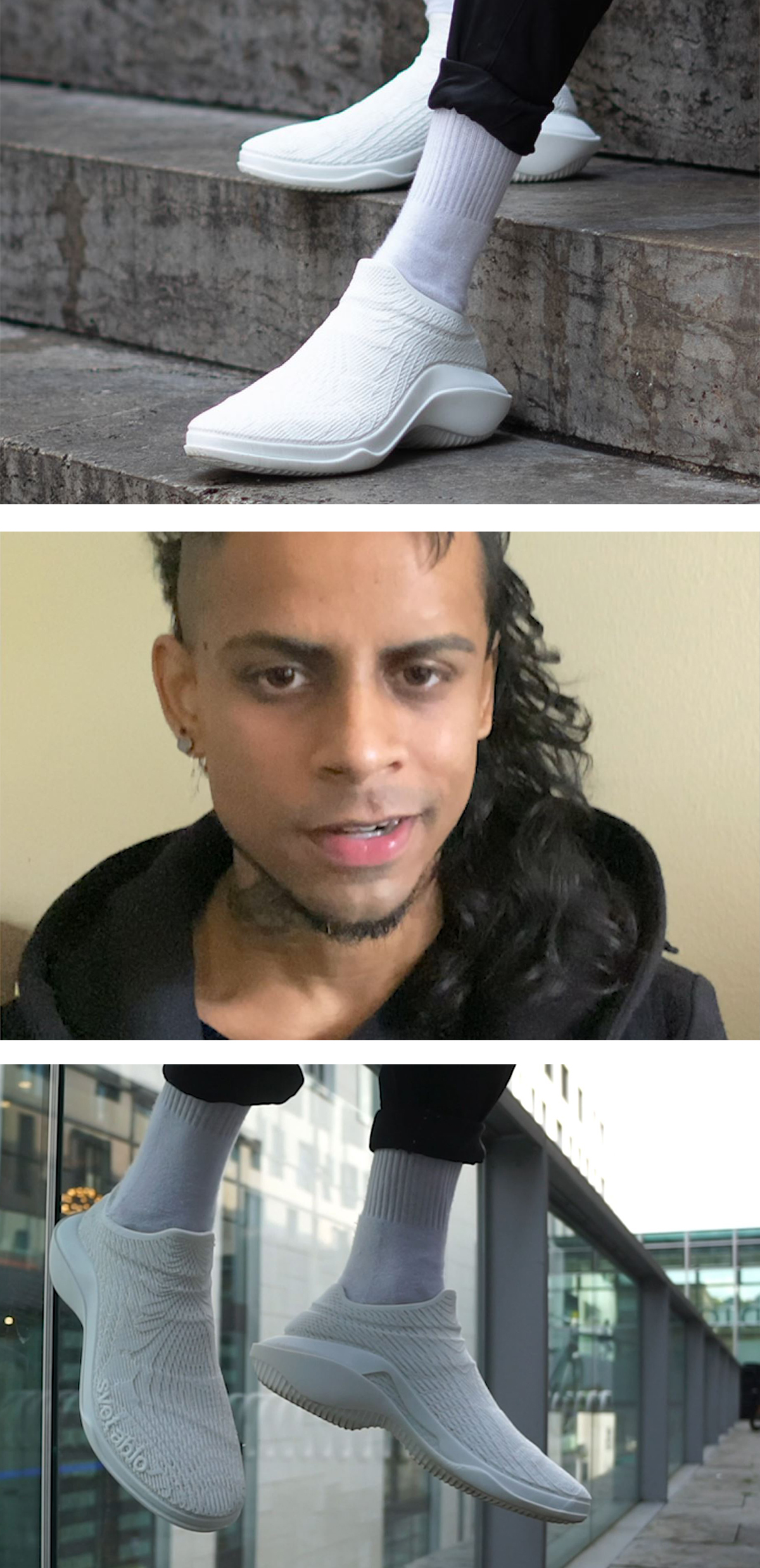
Es un zapato plenamente funcional fabricado con impresión 3D a partir de un escáner del pie. El zapato al completo se imprimió de principio a fin eliminando así cualquier costura o pegamento. La suela, la entresuela y el empeine; todo se crea en un único proceso y con un material.
¿POR QUÉ?
El cambio climático y el medio ambiente son dos de las grandes preocupaciones en este 2020 y yo realmente creo que el calzado realizado con impresión 3D usando materiales reciclados tiene un futuro alentador. El zapato en su totalidad está fabricado con un único material TPU (dureza Shore A 60). Los zapatos se podrían llegar a fundir y reusar el material para imprimir zapatos nuevos. Además, no se necesitan las hormas tradicionales puesto que el modelo se desarrolla directamente a partir de un diseño en CAD.
IMPACTO DESPUÉS DE LA COVID
El impacto reciente de la pandemia a nivel mundial ha provocado unas pérdidas de ingresos considerables a algunos fabricantes de calzado. Las cadenas de suministro de una gran parte de estas marcas están en Asia y otros países con economías débiles donde se explota a los trabajadores a cambio de salarios mínimos. Estos zapatos impresos con tecnología 3D se podrían fabricar a nivel local eliminando así la necesidad de tener grandes infraestructuras o naves de producción. Además, en comparación con la forma tradicional, no habría un exceso de producción.
Mención especial: Tactile Compass for colours
Taktilesdesign GmbH I Sylvia Goldbach I Eric Bahr

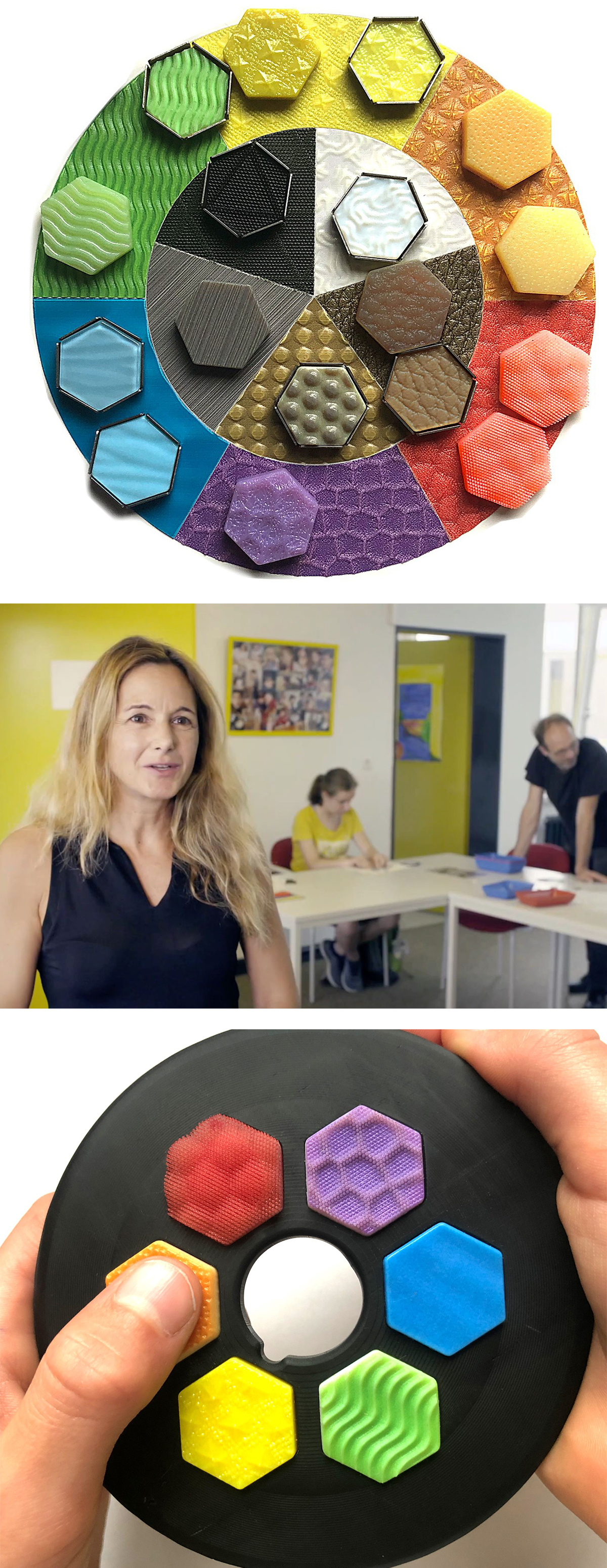
Formato/Diseño
La brújula táctil de color nos lleva a un nuevo mundo de percepción. Consigue guiar a los usuarios a través de paisajes, fotografías y objetos diarios. Las superficies de la brújula están creadas con la tecnología de estereolitografía de baja fuerza (LFS) para aproximarse a la naturaleza y asociaciones. Taktilesdesign añade además elementos específicos. La referencia a la brújula clásica y a la rueda de color sirve para facilitar la asociación como guía y orientación. Al igual que ocurre en la naturaleza, las superficies táctiles con distintos grados de dureza, a través de materiales cálidos y fríos hacen justicia a los colores en la representación. Las elevadas exigencias que conlleva la producción de las distintas propiedades en un único proceso solo es posible con la última generación de impresión 3D.
Grado de innovación
¡Todavía no existe un código universal de colores! Un nuevo lenguaje de experiencia táctil para personals invidentes genera al tacto una sensación harmónica innovadora. La textura asumirá la función comunicativa, independientemente del idioma.
Potencial para la fabricación aditiva
El grupo particular de usuarios justifica una tirada menor. Las pequeñas partes hexagonales pueden cubrir huecos de construcción con eficacia. Se emplean un nutrido grupo de materiales. Nuestra brújula no se puede fabricar de otra manera que no sea la fabricación aditiva debido al primer paso de combinar modelos con texturas de gran nivel y colores con los últimos materiales de Stratasys y la impresión de Roland UV.
Potencial económico
La inclusión de un sector desfavorecido de la población en la esfera pública es un motivo de interés social. El 80% de los invidentes son mayores de 50 años. La tendencia está en alza debido al abuso de pantallas en la infancia temprana.
Encontrará más información sobre Tactile Compass for colours en este vídeo:
https://youtu.be/gvsf65xsqTs/
Premio de innovación: ANAMOS heart model
ANAMOS UG (haftungsbeschränkt) I Lehrstuhls FAPS, FAU Erlangen-Nürnberg I Wacker Chemie AG I Hannah Riedle I Anna Seufert

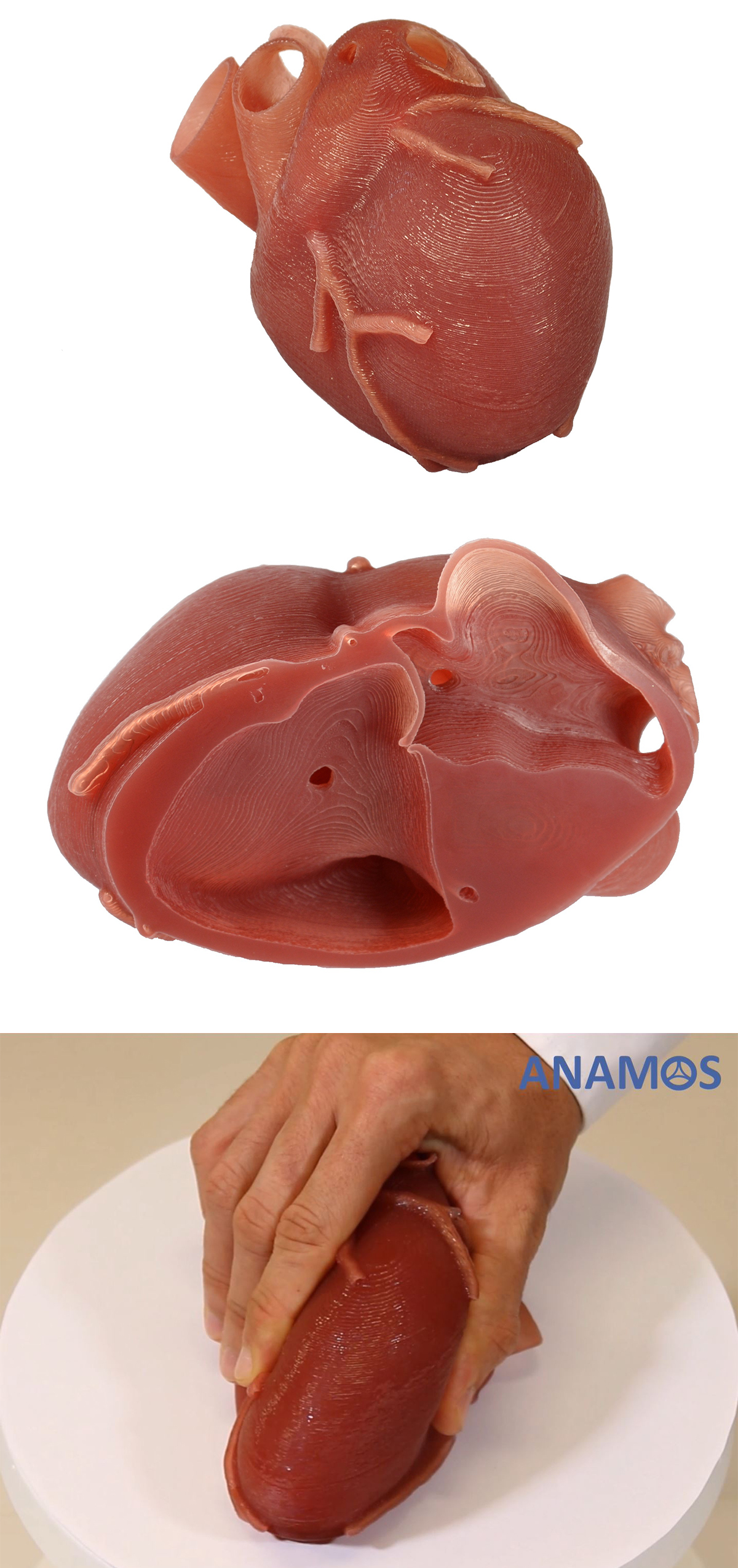
Este modelo anatómico de corazón humano, con una función y un tacto realistas, se ha producido con procesos de fabricación aditiva y ofrece nuevas oportunidades para la simulación quirúrgica. Como sustituto para aplicaciones directas que requieran un cuerpo humano, hace posibles nuevos escenarios de ensayo y evaluación, mejorando la eficiencia del aprendizaje, el desarrollo de productos médicos y la investigación. Al contrario que los modelos biológicos, como los cuerpos humanos o animales, los modelos artificiales ANAMOS siempre están disponibles, son fáciles de almacenar y manejar, y pueden recrear cualquier anatomía o afección. Los modelos de corazón ANAMOS son producto de un novedoso método de diseño genérico que integra datos de imágen de TC que permiten que se recreen de manera realista los ventrículos y las aurículas del corazón, así como todos los vasos y arterias coronarias que lo rodean. El modelo se centra en la funcionalidad realista, y es la razón por la que cuenta con un diseño único de válvulas anatómicas y estructuras de vasos sanguíneos huecas. Para su fabricación aditiva se emplean siliconas y la tecnología ACEO® (Wacker Chemie AG, Múnich) que permite recrear las propiedades elásticas de los tejidos del corazón y a la vez mantener la complejidad geométrica. Cuando no están en una situación de estrés, las válvulas del modelo de corazón ANAMOS tienen huecos pequeños. Sin embargo, cuando se ejerce una fuerza en la dirección del flujo sanguíneo, las válvulas elásticas se abren hacia la pared del corazón o de los vasos sanguíneos. Sin embargo, si se ejerce una fuerza en dirección contraria al flujo sanguíneo, las válvulas se comprimen y cierran el hueco. Esta funcionalidad es posible gracias a la combinación única de un enfoque de diseño genérico, la fabricación aditiva y el uso de silicona elástica; y hacen que esta propuesta sea realmente transgresora.
El diseño de este modelo se puede adaptar para recrear distintas afecciones. La versión expuesta presenta un modelo con un defecto septal auricular (una separación problemática entre las dos aurículas) en el lado izquierdo, y un defecto septal ventricular (una separación problematica entre los dos ventrículos). Las posibles aplicaciones para simulaciones quirúrgicas incluyen la navegación intraoperativa, la sustitución de válulas caridacas patológicas y el cierre de defectos septales. Un estudio científico ha confirmado la precisión anatómica necesaria, la compatibilidad con técnicas de imagenología como la ecografía y el ecocardiograma, así como su funcionalidad en la simulación quirúrgica.
Historia
El concepto para el modelo tiene su origen en el proyecto de investigación “Silicone Biomodels” desarrollado de manera conjunta por la Facultad de Automatización de la Producción y Sistemas de Producción de la Univesidad de Erlangen-Núrembeg junto a Wacker Chemie Ag. A raíz de este estudio surgió en el año 2020 el proyecto “SofTiss Anatomics” que recibe financiación del programa de becas del fundador de EXIST. Como apoyo al proyecto, en agosto del año 2020 se fundó ANAMOS UG (sociedad limitada) para desarrollar y distribuir los modelos anatómicos impresos con tecnología 3D en el sector de la medicina y el equipamiento médico.
Diseño basado en la simulación: Bolt it
ETH Zürich I Inspire AG I Gressel I Julian Ferchow I Marcel Schlüssel

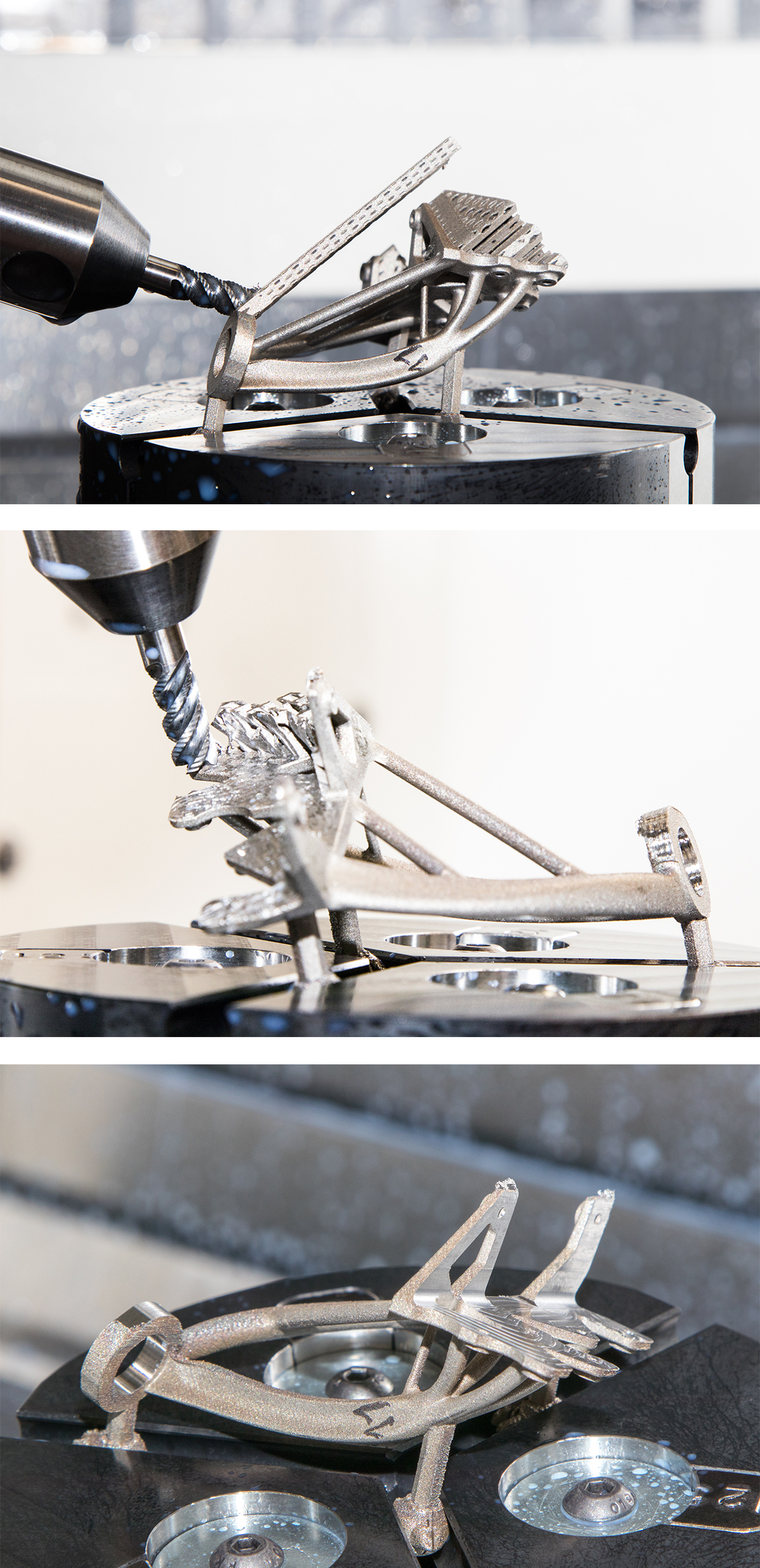
El concepto de BOLT-IT hace posible una cadena de posprocesamiento automatizada, digital y física. BOLT-IT son interfaces universales, producidas en el proceso de fabricación aditiva (AM). Facilitan el agarre y manejo automático de los componentes de fabricación aditiva. La posición de los componentes es conocida en CAD, por lo que no son necesarias otras referencias. Además, se posibilita un mecanizado robusto con accesibilidad por cinco lados. La extracción de las interfaces con una torsión simple completa el proceso. El proyecto se llevó a cabo como parte de una colaboración de I+D entre Inspire AG, ETH Zurich y Gressel. El proyecto de dos años recibió financiación de Innosuisse y contó con el liderazgo de Julian Ferchow (investigador asociado de Inspire AG, ETH Zurich) y Marcel Schlüssel (Jefe de tecnología de Gressel).
En este enlace encontrará un vídeo con más información:
https://www.youtube.com/watch?v=i3TioiUHCOE&t=2s/
Newcomer Prize: Adaptive splint
School of Design Innovation, Victoria University of Wellington I Yejun Fu


Se han llevado a cabo varios proyectos para desarrollar el rendimiento de materiales reactivos o para explorar las estructuras geométricas para este tipo de materiales con el objetivo de configurar productos que se puedan beneficiar de esta transformación. Los precedentes en el ámbito médico muestran un gran potencial para combinar materiales de origen biológico con la impresión 4D a la hora de fabricar productos altamente individualzados que se adaptan a la forma, el movimiento y los requisitos psicológicos del cuerpo humano.
Este proyecto comenzó desarrollando polímeros reactivos imprimibles con base biológica con el fin de contribuir con la experiencia en diseño industrial en un grupo multidisciplinar de científicos de materiales e ingenieros como parte del Desafío Nacional de Ciencia (NSC) Portfolio 5 Spearhead Project “Fabricación aditiva e impresión 3D y 4D de biocompuestos”. https://www.sftichallenge.govt.nz/ourresearch/projects/spearhead/additive-manufacturing-and-3d-and-or-4d-printing-of-bio-composites/
El proyecto exploraba la posibilidad de vincular la impresión en 4D para la fabricación de este tipo de accesorios que uno se pone usando como ejemplo una férula de muñeca adaptable para la rehabilitación progresiva. Para ello se desarrolló una investigación sobre los procesos de curación de heridas y los métodos de rehabilitación relacionados para determinar la funcionalidad necesaria de la férula y sobre las estructuras biológicas relevantes como inspiración para la geometría del diseño.
Puesto que se trabajó con científicos de material, el diseño se desarrolló en dos direcciones. La primera fue usar los nuevos polímeros experimentales y probar la capacidad de respuesta para configurar una capa de la férula que fuera imprimible, cambiara de forma y se adaptara a los cambios en la muñeca durante el proceso de curación. La segunda fue integrar estos experimentos en modelos 3D de una férula adaptable constituida por tres capas que respondiera a los requsitos de la rehabilitación progresiva. Esta investigación desafía las propiedades de los nuevos materiales y de los procesos de impresión asociados; aunque será necesario llevar a cabo más estudios para mejorar tanto la impresión como la capacidad receptiva. Sin embargo, el diseño de la férula ofrece un caso práctico para posibles aplicaciones en el ámbito extenso de este tipo de recursos que incorpora capas múltiples de materiales reactivos y geometrias diferentes que se pueden adaptar a las necesidades del cuerpo humano.
Para más información, visite el siguiente enlace: https://www.behance.net/gallery/84896425/An-adaptive-splint-Masters-project
Encontrará más información sobre Adaptive splint en este vídeo: https://vimeo.com/356800439/
Premio del público: A.I. Bindings
Addition I Saulo Armas I Oriol Massanes I NOW I Nidecker Group

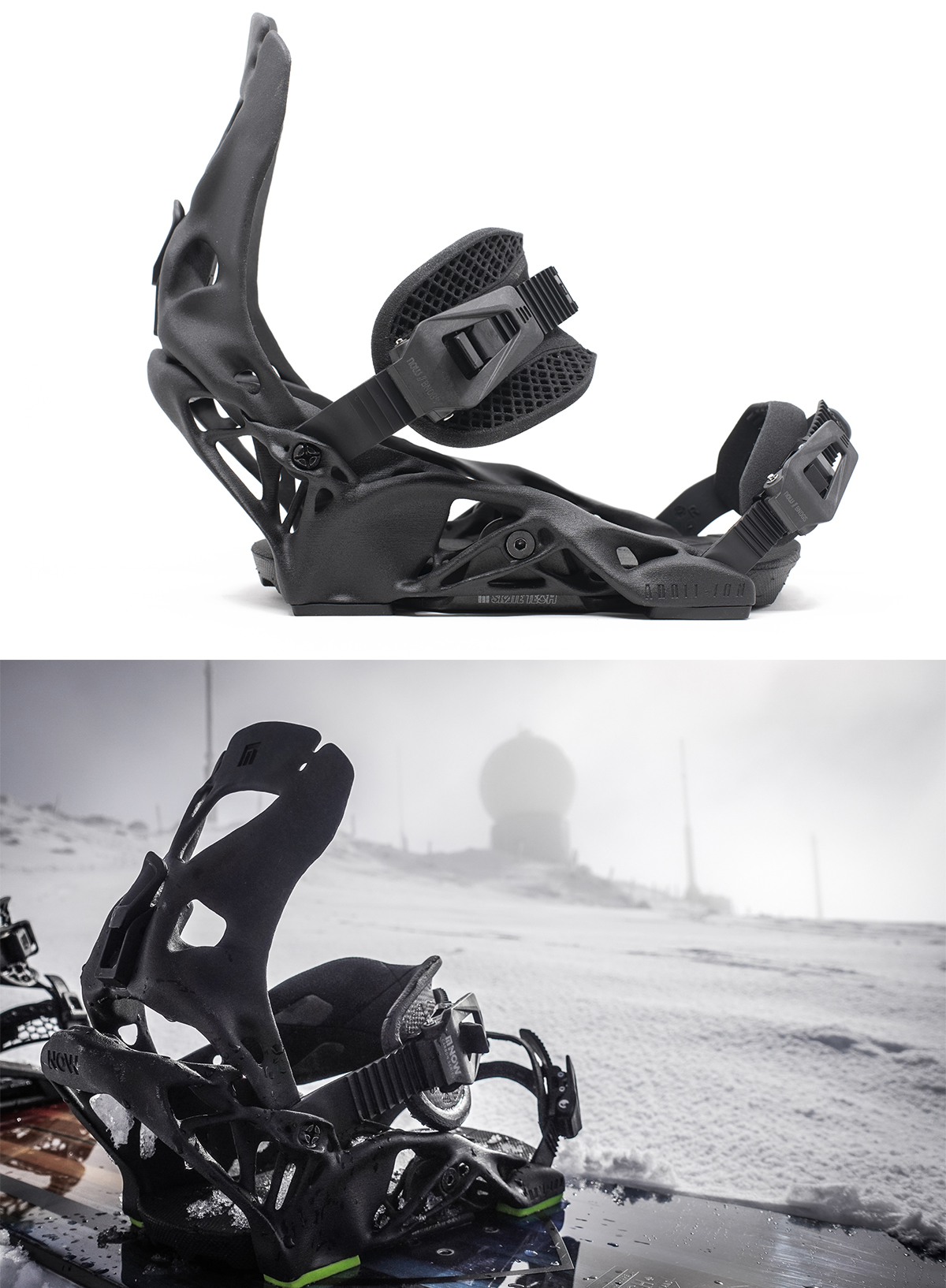
Para desarrollar una fijación flexible, optimizada para realizar giros, teníamos que proporcionar la máxima rigidez con el menor peso posible. Y para poder llegar a ello, Addit-ion contribuyó con su dominio de la inteligencia artificial e impresión 3D. NOW aportó su tecnología patentada Skate Tech z Nidecker Group su vasto conocimiento para combinar tecnologías.
Primero construyeron de manera conjunta un caso de carga que podía emular el estrés que sufren las fijaciones cuando se somenten a procesos agresivos de torneado y tallado; y posteriormente usaron una representación mecánica mínina de Skate Tech para general la forma final a su alrededor usando el diseño generativo de Autodesk.
Tenían docenas de resultados diferentes para comparar, con distintos materiales y tecnologías, pero tras muchas horas de simulación y análisis de datos, conseguimos la mejor opción de impresión con PA12.
Peso completo de la tabla - ~5kg
Peso de las fijaciones - 1600gr
Estos son los finalistas de este año:
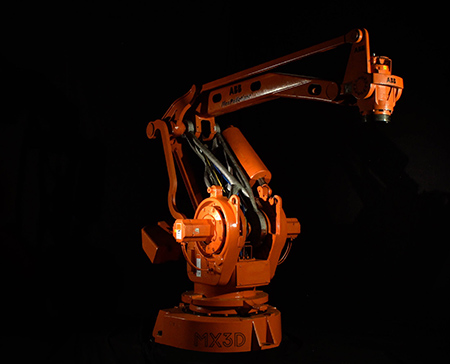
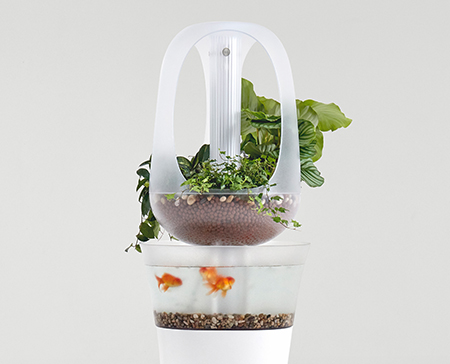
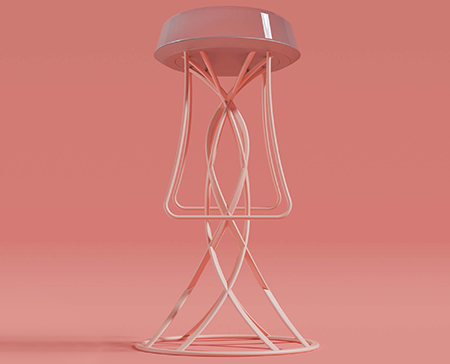
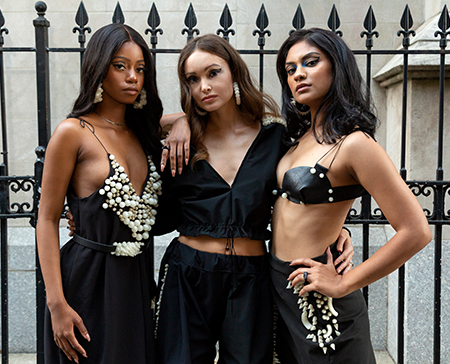
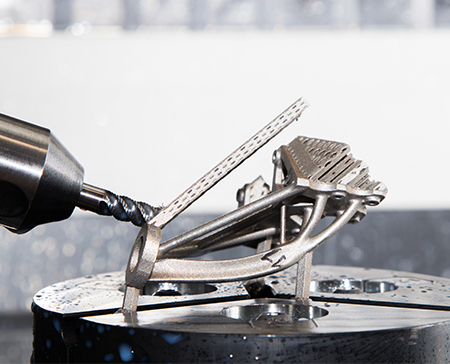
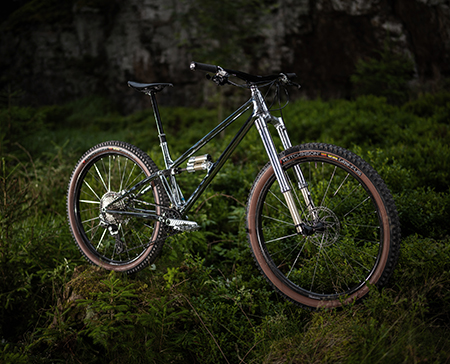
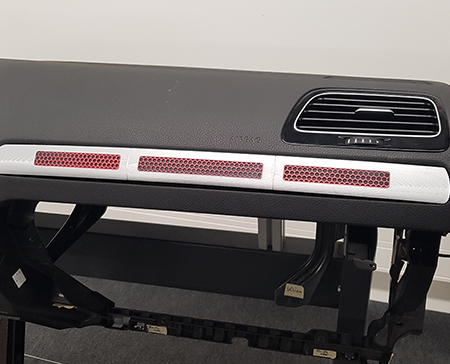
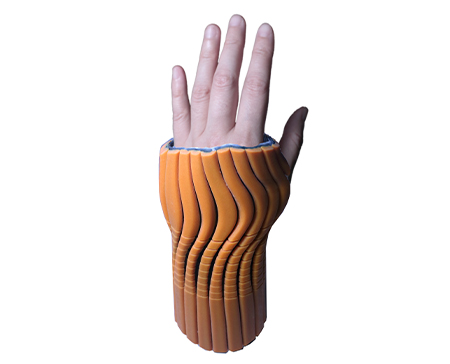
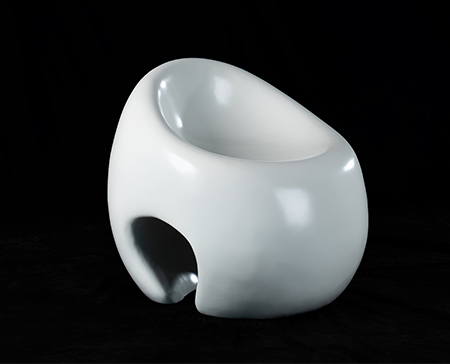
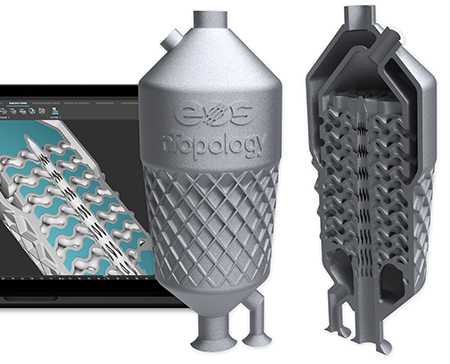
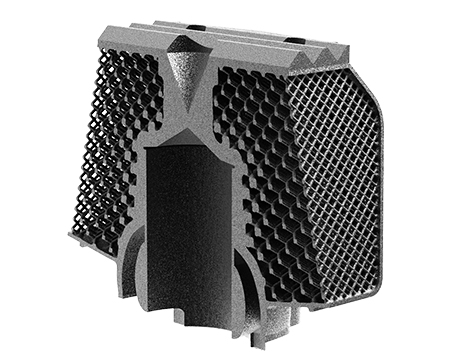
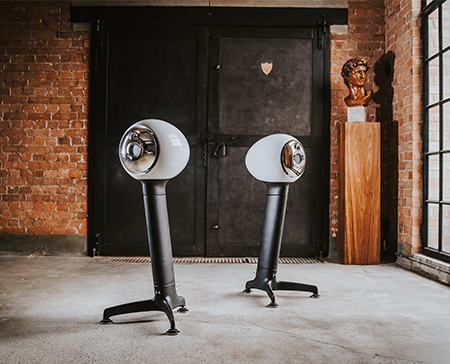
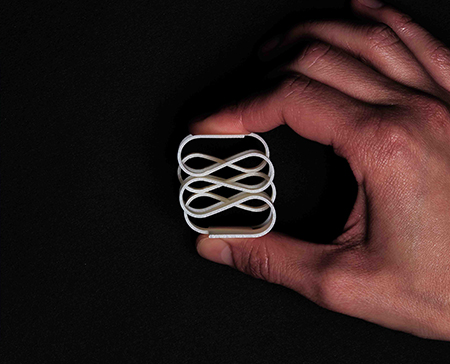
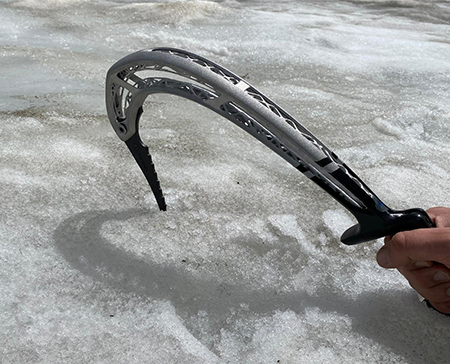
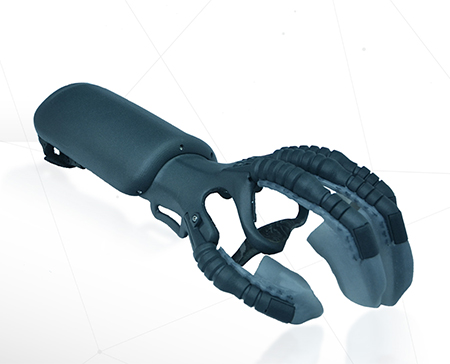
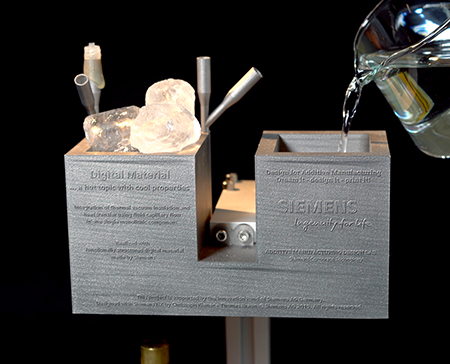
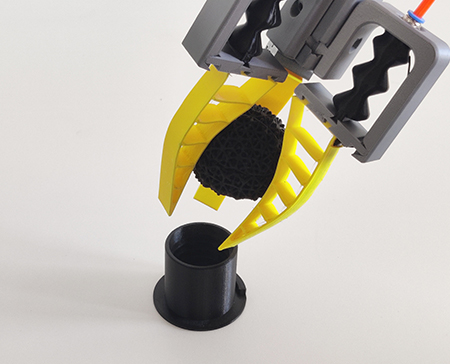
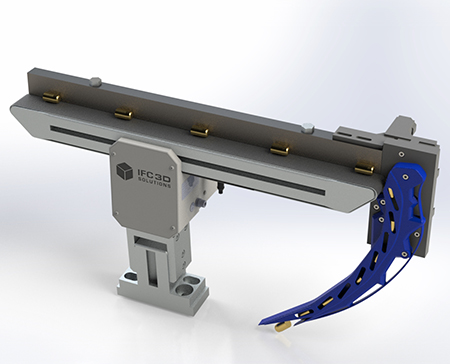
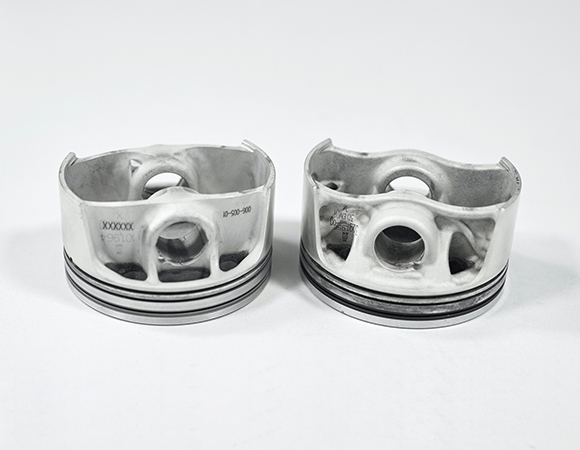
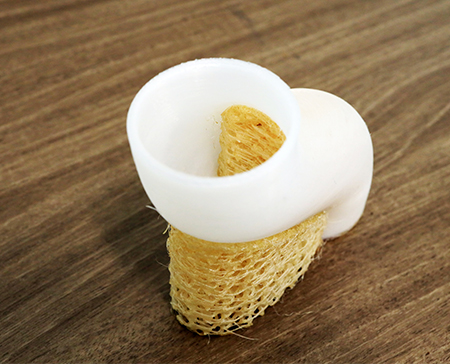
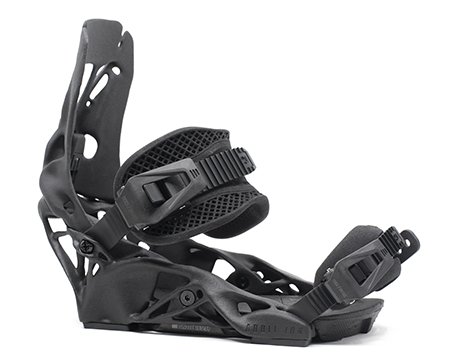
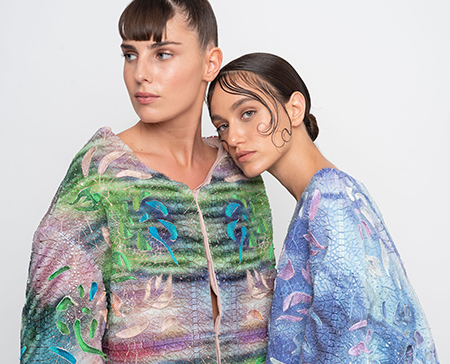
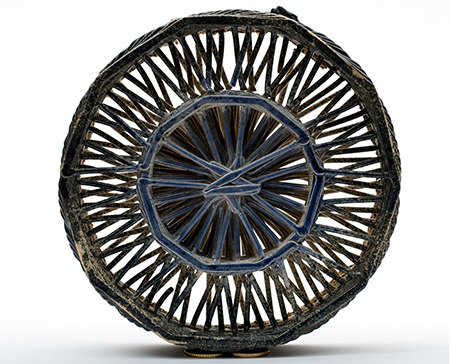
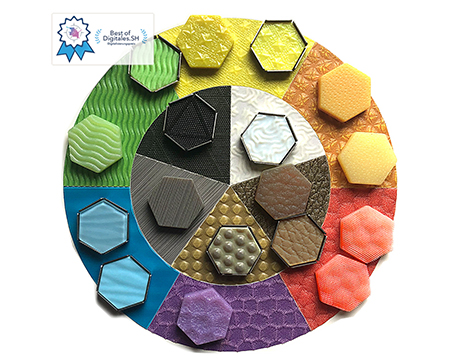
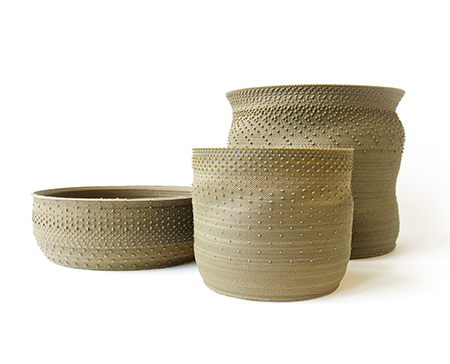
×
Finalistas de los folletos: Los finalistas de la purmundus challenge 2020 [pdf: 11,0 MB]
Vote por su favorito. Aquí puede acceder a la votación: https://pollunit.com/polls/purmundus_challenge_2020_public_choice_award
!Desde aquí nos gustaría dar las gracias al jurado y a los colaboradores!
Juardo 2020
Christoph Behling - Christoph Behling Design Ltd.Prof. Richard Bibb - Loughborough University
Isabelle Fröhlich - Volkswagen AG
Tilla Goldberg - Ippolito Fleitz Group GmbH
James Helliwell - hyperTunnel Limited
Dr. Alexander Hildebrandt - Festo AG & Co. KG
Frank Kleemann - Freelance industrial designer
Andreas Pany - Ernst Strassacker GmbH & Co. KG
Prof. Dali Sun - Beijing University of Technology
Graham Tromans - G. P. Tromans Associates
Dr. Clara Usma - Deakin University