
Por séptima vez se ha otorgado el premio de diseño en impresión 3D y 4D del purmundus challenge durante la feria Formnext en Francoforte del Meno el pasado 21 de noviembre de 2019. Un total de siete candidaturas recibieron el preciado trofeo dorado.

En 2019 el purmundus challenge mandó un claro mensaje de calidad al sector de la impresion 3D y 4D. Según apunta Corinna Ray, directora del purmundus challenge, „la fabricación aditiva se emplea de una manera más innovativa y más enfocado en la aplicación que en años previos“. Las ideas premiadas muestran la perfecta interpretación de las dimensiones de la estética y la funcionalidad. „Actualmente la impresion 3D y 4D facilita la creación de formas únicas que no se pueden lograr con otros medios“, anade Christoph Behling, Christoph Behling Design Ltd., miembro del jurado del purmundus challenge. Empresas, industria, universidades, estudios de diseño y empresas de nueva creación se identifican hoy en día más que nunca con la impresión 3D y 4D como tema clave de la industria en el tejido económico.

Bajo el lema „Más allá de la impresión 3D“, los 38 finalistas de 18 países diferentes de los cinco continentes dieron a conocer sus extraordinarias creaciones del 19 al 22 de noviembre de 2019 en Formnext, la feria líder del sector. Mostraron su punto de vista e ideas sobre cómo se pueden crear productos individualizados y cuál es el papel que la impresión 3D y 4D juega en ello.
This year’s winners are:
1er premio: Stealth Key
UrbanAlps AG I Dr. Alejandro Ojeda


¿Tenía usted idea de que las llaves de alta seguridad ya no son seguras? Su empresa puede sufrir ataques. La cíbercriminalidad representa una amenaza. Con razón son muchas las empresas que se protegen de ello y cuentan con mecanismos innovadores de defensa y personal espezializado. Las nuevas opciones de escaneado e impresión 3D generan un nuevo problema físico: los robos en oficinas, laboratorios e incluso en la sala de servidores. Sin rastro. ¿Cómo es posible? Cualquier llave mecánica de seguridad con hendiduras y agujeros visibles se puede replicar. Usando la tecnología más avanzada se pueden escanear y replicar sin autorización incluso llaves de seguridad con clavijas interactivas. Dentro de no mucho cualquier persona va a poder hacer copias de llaves convencionales.
Este problema de seguridad se soluciona con ayuda de la tecnología furtiva.
La tecnología furtiva utiliza las posiblidades de la impresión 3D industrial con metales para ofrecer una protección anticopia segura contra reproducción de llaves. La tecnología punta que emplea UrbanAlps se utiliza también para la producción de componentes altamente resistentes para satélites, motores a reacción y turbinas de gas.
La tecnología furtiva ofrece una protección en cuanto a seguridad a un nivel superior con un sustema físico de llaves y cilindros entre los que se esconde el código entre los rebordes finos y robustos para evitar así copias no autorizadas. Para nuestros clientes esto significa tener la seguridad de que su llave de alta seguridad no va a poder ser escaneada y que funciona independientemente de los sistemas digitales. Nuestras soluciones líderes en el mercado se pueden usar para actualizar puertas y cerraduras ya existentes evitando así daños mecánicos. Las llaves se fabrican con tecnología aeroespacial moderna. No hay llaves en bruto, electrónica o imanes. Realmente inteligente. Sencillamente novedoso.
Códigos ocultos
La tecnología furtiva utiliza la tecnología de impresión 3D con metal para crear una llave física en la que los códigos están completamente ocultos, lo que garantiza la máxima protección anticopia. Gracias a los códigos ocultos en los finos bordes se garantiza que el código de seguridad no se pueda ni fotografiar ni escanear. Las llaves se fabrican y codifican de manera individual.
Tecnología pionera de Suiza
Está desarrollada por ingenieros suizos con conocimientos de la tecnología aeroespacial, la avanzada tecnología furtiva de UrbanAlps aúna una ingeniería inteligente con artesanía innovadora y detallista para conseguir un nivel de seguridad incomparable. Todas las llaves y cilindros mecánicos de la empresa, así como en todos los candados furtivos de superaleación de la empresa
Solución puramente mecánica
Las llaves furtivas se fabrican con fundición láser capa por capa con superaleaciones. Es la misma tecnología que se emplea para la producción de componentes de alta resistsencia para los motores a reacción y turbinas de gas. Esta solución puramente mecánica no requiere de electrónica o imanes; simplemente de mecánica inteligente, sencilla y fiable.
Soluciones fiables
Las últimas medidas de seguridad de las llaves convencionales tampoco ofrecen ninguna garantia contra copias no autorizadas con impresoras 3D. Este peligro hace que las empresas tengan que introducir costosos sistemas de seguridad electrónicos. Con ello aumente por desafortunadamente el riesgo de problemas de fiabilidad y surgen además riesgos adicionales debido a la vulnerabilidad digital. Es por ello que en algunos ámbitos de seguridad no se recomienda el uso de llaves que requieran microprocesadores, acceso a redes, baterias u otros sistemas digitales. La llave furtiva patentada ofrece la mayor protección anticopia que se puede usar de manera aislada o en combinación con nuestras soluciones digitales.
Un socio fiable
Desarrollado en laboratorios con ingeniería avanzada de Zúrich (Suiza)la llave furtiva patentada de UrbanAlps emplea tecnología de impresión 3D de metales. Es por ello que damos importancia a una producción de calidad para poder alcanzar este nivel especial de seguridad.Las llavesfurtivas funcionan como las llaves mecánicas convencionales, pero al contraio que las llaves planas, su diseño innovador ofrece una protección considerable contra copias sin autorización.Los cilindros específicos para cada cliente se adaptan a los perfiles estándares europeos, escandinavos y estadounidenses.
Autentificación de doble factor como por ejemplo microprocesadores y sensores, se pueden incorporar a las soluciones furtivas. La ventaja principal es el perfil de seguridad independiente de las llaves. Actualmente participamos en diversos proyectos en toda Europa con empresas interesadas en actualizar sus soluciones de seguridad con tecnología furtiva. Disponemos de oficinas en Zúrich, Dubai, la República Checa garantizan el rápido crecimiento de UrbanAlps AG para poder hacer frente a la creciente demanda. Nuestra inusual estructura empresarial nos facilita ofrecer flexibilidad y escalabilidad a las empresas que necesitan depositar toda la confianza en las llaves mecánicas como parte de su arquitectura de seguridad.
Producción en serie basada en láser
- producción exclusiva en fábricas de alta tecnología
- marcaje de llaves individual
- fabricacion especial de los cilindros
- Sistemas de cierre y opciones con el mismo cierre
- Cabeza de colores para facilitar el marcaje individual
2º premio: Hydrophytes - 4D Printing
Victoria University of Wellington I Nicole Hone


Los diseños se han creado en 3D con Rhino y Grasshopper de YBrush. Con estos programas se facilita el control específico de la forma, la estructura de la superficie, la estructura interna y la combinación de materiales. Cada diseño dispone de una cámara sellada que le permite activarse de manera independiente a través del hinchado neumático. Para la película se conectan las impresiones 4D a una serie de bombas manuales, se sumergen en agua y se iluminan con colores usando un proyector LED. En el contexto de la película, los hidrófitos alentan a pensar sobre la calidad futura de nuestro clima y el papel del diseño para unir al hombre con la naturaleza. Estos objetos generados con ordenador (CGO en sus siglas en inglés) utilizan tanto el mundo digital con su variedad y eficciencia con respecto al modelado, así como el mundo físico en el que los objetos pueden interactuar con el entorno, las personas y otros objetos impresos.
Los hidrófitos interactúan de manera natural. Los movimientos se corresponden con las „reglas“ de la vida real y no con las de la animación por ordenador. El proyecto acerca el mundo físico y digital para diseñadores y público. Con los atractivos efectos visuales que se pueden apreciar en el vídeo, se despierta el interés por tocar la pantalla. Los hidrófitos representan el nuevo concepto de la animación tangible que hace que objetos cobren vida en el mundo del público usando la impresión multimaterial 4D. Esta nueva técnica es decisiva para la industria cinematográfica y las exhibiciones en la que está de moda los mundos temáticos inmersivos. Los decorados de película creados con esta tecnología podrían ayudar a provocar reacciones reales de los actores. La „magia“ del cine se puede trasferir a encuentros físicos y auténticos en parques temáticos. Así mismo, experiencias multisensoriales en centros de educación, como museos o acuarios, también serían factibles.
Este proyecto demuestra cómo el mundo de la impresión 3D/4D se adentra en un terrero interesante en el que se pueden recrear objetos con características compositivas y dinámicas similares a las presentes en la biología natural. Para poder ver los hidrófitos acceda a este enlace: http://vimeo.com/nicolehone/hydrophytes-4d-printing.
El vídeo es fiel al original, sin los efectos añadidos en postproducción.
3er premio: Monolithic Rocket Chamber
CellCore GmbH I Dr. Paul Schüler I Andreas Krüger


Para demostrar el potencial y las ventajas para el espacio de la impresión 3D en camas de polvo metálico, Cell Core GmbH desarrolló junto con SLM Solutions Group AG un prototipo de motor de cohete que en un diseño integral aúna el suministro de combustible, el inyector y la camara de empuje en combinación con un innovador concepto de refrigeración de la estructura.
El elemento principal de este prototipo es la estructura de malla con optimización funcional que se encuentra integrada en la pared del motor de combustión; la cual además de cumplir con la capacidad de carga necesaria, ofrece distintas posibilidades de refrigeración al evacúar de manera eficiente el calor de las paredes interiores de la cámara de empuje gracias a la circulación activa del hidrógeno líquido. Las características de este refrigeramiento estructural superan notablemente a los planteamientos convencionales; como, por ejemplo, los conductos concéntricos labrados de refrigeración. Ofrece una relación óptima entre estabilidad y la cantidad de material empleado; y presenta una resistencia aerodinámica menor con una superficie de reacción a su vez mayor. No es que sea más eficiente, si no que además integra funciones adicionales. El hidrógeno que circula a través de la estructura de refrigeración se mezcla después con el oxígeno en la parte superior del motor de propulsión, es conducido a través de las numerosas cabezas de injección a la cámara de combusitón para que después se produzca la combustión usando un elemento de las bujías de ignición.
Diseño con fabricación optimizada
A la hora de construir el motor de combustión se tuvo en cuenta que la producción se pudiera realizar unsando la menor cantidad posibles de estructuras de soporte que necesitaran después un trabajo de postproducción costoso. Con respecto a esto, SLM Solutions colaboró en el proyecto con el diseño técnico de producción de las piezas más complejas para prepararlo para el proceso de fusión selectiva por láser (SLM); tales como el desarrollo de parámetros específicos para la geometría de las piezas – inclusive también la optimización de revestimientos interiores o la orientación óptima de las piezas en la cabina de impresión. Para evitar errores se identificaron además sectores críticos en las piezas y con ayuda de pruebas de impresión reducidas se determinaron parámetros de especificación relevantes para las adaptaciones de diseño. Para podercumplir con los requisitos materiales del sector aeronáutico y espacial, se fabricó el motor de combustión con la aleación de níquel y cromo IN718 en la impresora de fusión selectiva por láser SLM®280.
IN718 es un material endurecible por precipitación que tiene una excelente resistencia de tracción, fatiga, deslizamiento y rotura hasta los 700°C y que ya ha sido validado con éxito en escenarios de aplicación aditivos reales. Esto convierta al IN718 en una aleación relevante para los componentes de aviación y de las turbinas de gas, así como para diversas aplicaciones con altas temperaturas, como por ejemplo, los motores de los cohetes. Con los métodos de elaboración convencionales, éste es un material de difícil mecanizado que conlleva un alto desgaste de las herramientas. Gracias a la fabricación aditiva se minimiza el coste de postproducción de los componentes a pesar de tener estructuras complejas; y del mismo modo se evita el alto desgaste de las piezas.
Fueron pocas las iteraciones necesarias para crear el diseño final que con ayuda de la tecnología SLM® facilita la producción de piezas complejas en un periodo de tiempo de tan solo 5 días laborables. Este proyecto demuestra el enorme potencial para ahorrar costes que pueden ofrecer la fabriación aditiva junto con el diseño optimizado si lo comparamos con el tiempo de fabricación convencional (entorno a los seis meses) de un motor similar.
Mención especial: 3D-Printed Curtain Comfort Header
Diehl Aviation Laupheim GmbH I Andreas Henneberg


El marco confort de fijación de la cortina es una visión del futuro. El marco confort de fijación de la cortina como pieza interna de la cabina es una costosa cubierta de la barra de la cortina para crear una separación acústica y luminosa entre las distintas clases en la cabina de pasajeros. Debido al diseño individualizado de las cabinas, estas piezas se caracterizan por tener una gran variedad de anchuras y por sus pocos requerimientos mecánicos. Las medidas máximas actuales son 1140 mm x 720 mm x 240 mm. Debido a su complejidad, los marcos de fijación de cortina se fabricaban inicialmente con materiales compuestos hechos a mano. Diehl Aviation consiguió imprimir esta pieza tan compleja con la técnica de impresión FDM en una impresora Stratasys Fortus 900mc con resina ULTEM 9085. Los marcos confort de fijación de la cortina creados con impresoras 3D ya estαn plenamente cualificados. Las cubiertas impresas en 3D para las barras de cortina se han convertido actualmente en la mayor pieza de fabricación con producción capa por capa para las aplicaciones de los espacios interiores de las cabinas. Los primeros ejemplares ya se han enviado y Qatar Airways los tiene en funcionamiento desde el primer trimestre de 2019.
Concepto
Diehl Aviation utiliza la impresora FDM Fortus 900mc de Stratasys con resina ULTEM 9085 para la fabricación del marco confort de fijación para cortinas. El material Ultem 9085 está certificado por la Agencia de la Unión Europea para la Seguridad Aérea (AESA) y por la Administración Federal de Aviación (en inglés, Federal Aviation Administration, FAA). La barra de cortina impresa en 3D cumple con todos los requerimientos de carga mecánica, con la normativa de fuego, humo y toxicidad, y de liberación de calor. Se concedió el certificado de liberación – Formulario 1 de AESA, para las cubiertas impresas en 3D para cubrir la barra de las cortinas. Con la utilización de la tecnología sin herramientas, Diehl Aviation consiguió un mayor grado de libertad para los constructores, además de plazos de producción menores. La integración de funciones, como por ejemplo, canales para cables, la señalización de las salidas de emergencia o abrazaderas de sujección especiales, ofrece un potencial considerable para el ahorro de costes. Los logotipos OEM o de las aerolíneas se pueden imprimir directamente en las piezas para conseguir un diseño personalizado para los clientes. Las barras de cortina impresas en 3D muestras sobre todo la realización de la fabricación en serie con impresión 3D de piezas complejas para la cabina interior, además de un alto grado de personalización.
En este enlace encontrará más información acerca del marco confort de fijación de cortina impreso en 3D: https://www.highlights-diehlaviation.com/en/3d-printing-for-complex-cabin-components/
Premio de innovación: 3D-printed miniaturized endoscope
Institut für Technische Optik, Universität Stuttgart I Andrea Toulouse


El producto que mostramos es un endoscopio en miniatura impreso con tecnología 3D que tiene un diámetro máximo de tan solo 500 µm. La punta de una fibra multinúcleo contiene un objetivo impreso con tecnología 3D. Cada punto de imágen se transfiere a través de uno de los centros del conjunto flexible de fibras. En el otro extremo de la fibra, que durante una intervención quirúrgica se encuentra fuera del cuerpo, se puede observar la imágen y grabar con un (vídeo)micorscopio. Este endoscopio en miniatura es tan pequeño que incluso entra por el ojo de una aguja o por una cánula; y es capaz de transmitir una imágen en color de uno al otro lado de la fibra.
El micro-objetivo se fabrica por un proceso de polimerización con dos fotones en la impresora 3D „Photonic Professional GT“ (Nanoscribe GmbH). Esta técnica de impresión 3D se caracteriza por el minúsculo tamaño de los vóxeles de aproximadamente 150 a 450 nm. Así se pueden imprimir con una gota de fotobarniz pequeños volúmenes con calidad óptica y una gran precisión. En el siguiente paso del proceso se revela y se limpia el fotobarniz. Para este producto se emplea el proceso de polimerización con dos fotones para imprimir directamente en la punta de la fibra óptica multinúcleo. La montura de la lente y la apertura del sistema están concebidos de manera que conforman un sistema sofisticado de microcanales y agujeros que permiten que el fotobarniz líquido se pueda enjuagar tras la impresión 3D. En una fase de fabricación posterior se puede usar este sistema de microcanales también como depósito para tintas que no sean transparentes con la finalidad de aumentar aún más el contraste de la imagen.
El prodcuto que presentamos se puede expandir sin problemas. Se pueden añadir otros elementos al modelo 3D y se pueden imprimir conjuntamente casi sin coste alguno. Como el centro de la fibra puede transportar luz en ambos sentidos, se podría emplear una parte del conjunto para la iluminación. En este ejemplo se ha añadido al modelo 3D un sistema de guiado que conduce la luz hacia adelante en los núcleos externos. El halo de luz se dirige al objeto mediante la reflexión total y con la faceta final cóncava. A su vez se transmite al observador la imágen de dentro del conjunto de fibras en la dirección contraria. El endoscopio impreso en 3D tiene el potencial de superar a los aparatos convencionales fabricados en otros sectores. La libertad del proceso de producción se puede aprovechar al máximo para los diseños ópticos.
Las superficies de forma libre y los rebordes permiten al óptico desarrollar sistemas multilente de imágenes. Además del aumento y la reducción, el sistema está en condiciones de observar los objetos desde ángulos que en el caso de las lentes convencionales, conocidas como GRIN, serían inpensables. Por ello se espera que la gama de productos pensada se utilice en mercados nicho. Es obvio que estos sistemas tienen una gran importancia para nuestra sociedad por elevar las posibilidades técnico-médicas a otro nivel.
Este producto se ha desarrollado en el marco de un proyecto conjunto entre el Instituto de Óptica Aplicada (Prof. Herkommer) y el 4. Instituto de Física (Prof. Giessen) de la Universidad de Stuttgart.
Diseño basado en la simulación: KUPOL R1-0 (Motorcycle helmet)
KUPOL INC. I Gabriel Boutin


Lo que hace especial a esta nueva aplicación es la combinación de:
- Una carcasa dura con estructuras 3D integradas (material: HP 3D High Reusability PA 11)
- El material BASF ULTRASINT™ 3D TPU01 con un acabado satinado
- paredes y estructuras duras a pesar de ser finas (hasta 0,4 mm) fabricadas con la impresora HP Multi Jet Fusion (MJF).
En los cascos usuales hay bastante espacio entre la espuma de protección y la cabeza del usuario que se llena con tejidos acolchados altamente comprimibles para poder adaptarse a diversos tipos de cabeza; y por eso no se presta atención a la absorción de golpes o a la comodidad de uso. El acolchado cómodo de TPU de 15 mm de grosor y hecho completamente a medida que ofrece KUPOL utiliza esta cavidad para incorporar funciones de protección esenciales, como, por ejemplo, contra los impactos de baja velocidad o para la absorción de impactos oblicuos. Esto es algo que no se había conseguido hasta ahora con otras técnicas de fabricación. Además, este concepto también aborda el tema de cómo los usuarios se ponen el casco – con un proceso en dos fases para un manejo más fácil que con los cascos convencionales. Gracias a la separación entre la carcasa principal y el cómodo acolchado ya no es necesario ponerse o quitarse el casco haciendo fuerza para evitar hacerse daño en las orejas. El usuario simplemente se pone „el gorro“ de TPU y desliza a continuación la carcasa principal de PA11, lo que crea una mayor comodidad de uso y un producto final con protección mejorada. Además de las ventajas de comodidad y rendimiento del acolchado TPU, KUPOL tuvo costes de producción atractivos al imprimir las piezas plegadas. El resultado es impresionante: en doce horas se pueden producir cinco unidades completas en un solo trabajo de impresión con una impresora 3D HP Jet Fusion 5200.
KUPOL pudo mejorar el rendimiento del producto – sin embargo los costes de producción de la carcasa de PA11 son similares los costes de producción convenciones, como, por ejemplo, de los materiales compuestos de fibra de carbono. Gabriel Boutin, director ejecutivo de KUPOL, está convencido de que la impresión 3D va a cambiar la industria de equipamientos de protección. „Ofrece posibilidades infinitas para configurar el futuro de las protecciones corporales“. Para una empresa de I+D como KUPOL, La posiblidad de poder reaccionar en el día a día en función de las peticiones de sus clientes supone, en comparación con otras tecnologías, una gran ventaja para una empresa de I+D como KUPOL. La combinación de simulaciones mecánicas con pruebas físicas intensivas convierte a esta mejora vertiginosa en un grado de seguridad inimaginable.
Diseñador: Gabriel Boutin, KUPOL INC.
Nombre oficial del producto: KUPOL R1-0
Tamaño del producto: 347mm x 249mm x 251mm
Premio del público: 3D Printed Mountain Bike Frame
NMU ECO-CAR I Byron Blakey-Milner


Debido al alto coste de los materiales de gama alta para las bicicletas de montaña, este diseno puede competir económicamente sin problema con los diseños de de fibra de carbono de alta gama. Por otra parte, las herramientas de optimización topológica que se usan en este proyecto incrementarán la competitividad, ya que las impresoras 3D no están limitadas por los moldes de dos piezas como las bicicletas de carbono.
Por primera vez se va a imprimir una bicicleta sin junta de soldadura con el proceso de funcidión selectiva por láser (SLM). Esto le lleva a ser uno de los objetos metálicos impresos en 3D más grande de todos los tiempos
Estos son los finalistas de este año:
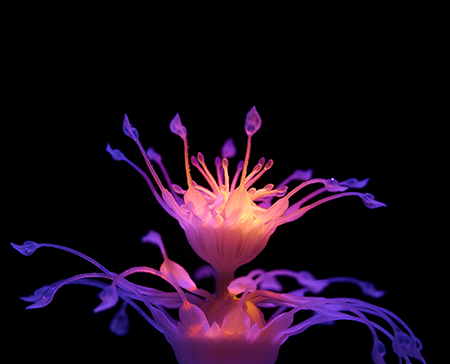
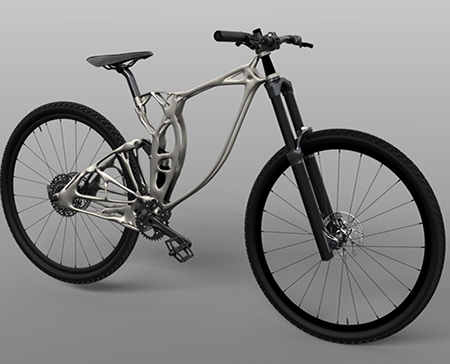



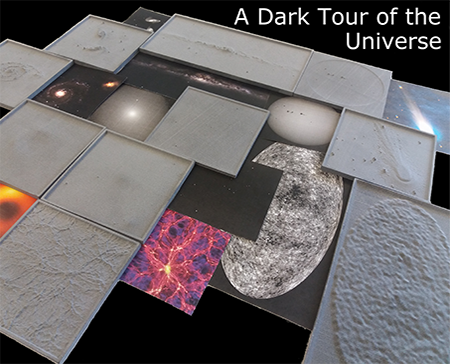



.jpg)


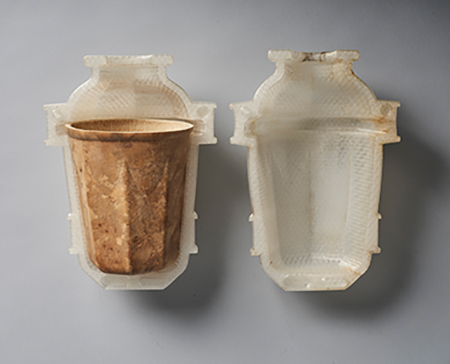

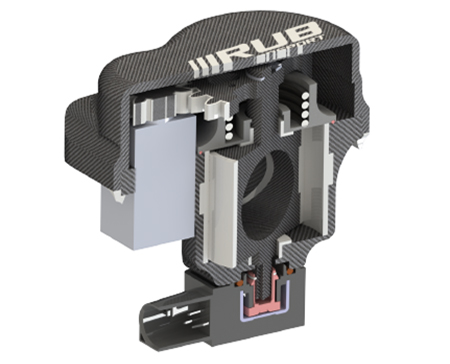


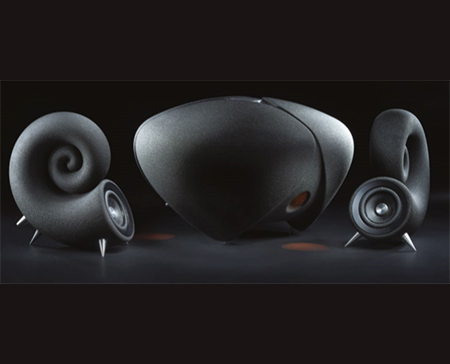
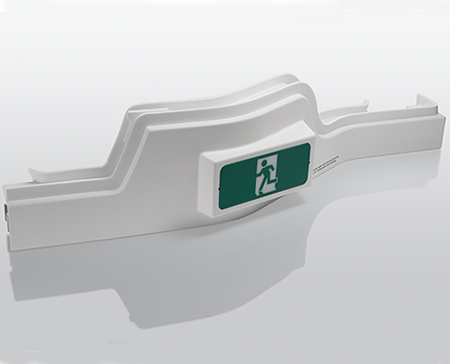






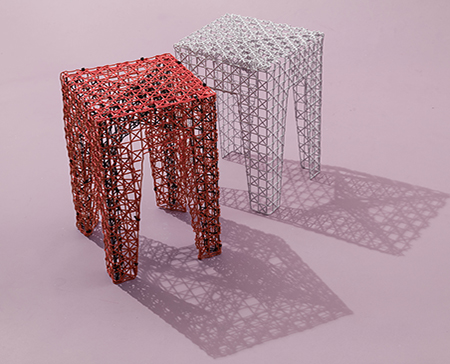









×
Finalistas de los folletos: Los finalistas de la purmundus challenge 2019 [pdf: 9,0 MB]
!Desde aquí nos gustaría dar las gracias al jurado y a los colaboradores!
Jurado 2019
Christoph Behling - Christoph Behling Design Ltd.Prof. Richard Bibb - Loughborough University
Isabelle Fröhlich - Volkswagen AG
Tilla Goldberg - Ippolito Fleitz Group
James Helliwell - hyperTunnel Limited
Dr. Alexander Hildebrandt - Festo AG & Co. KG
Frank Kleemann - Freelance industrial designer
Andreas Pany - Ernst Strassacker GmbH & Co. KG
Prof. Dali Sun - Beijing University of Technology
Graham Tromans - G P Tromans Associates
Dr. Clara Usma - Deakin University