
El 15 de noviembre de 2018 se entregó por sexta vez el premio de diseño en impresión 3D purmundus challenge durante la feria Formnext en Fráncfort. En total, seis de las propuestas obtuvieron el preciado trofeo dorado.
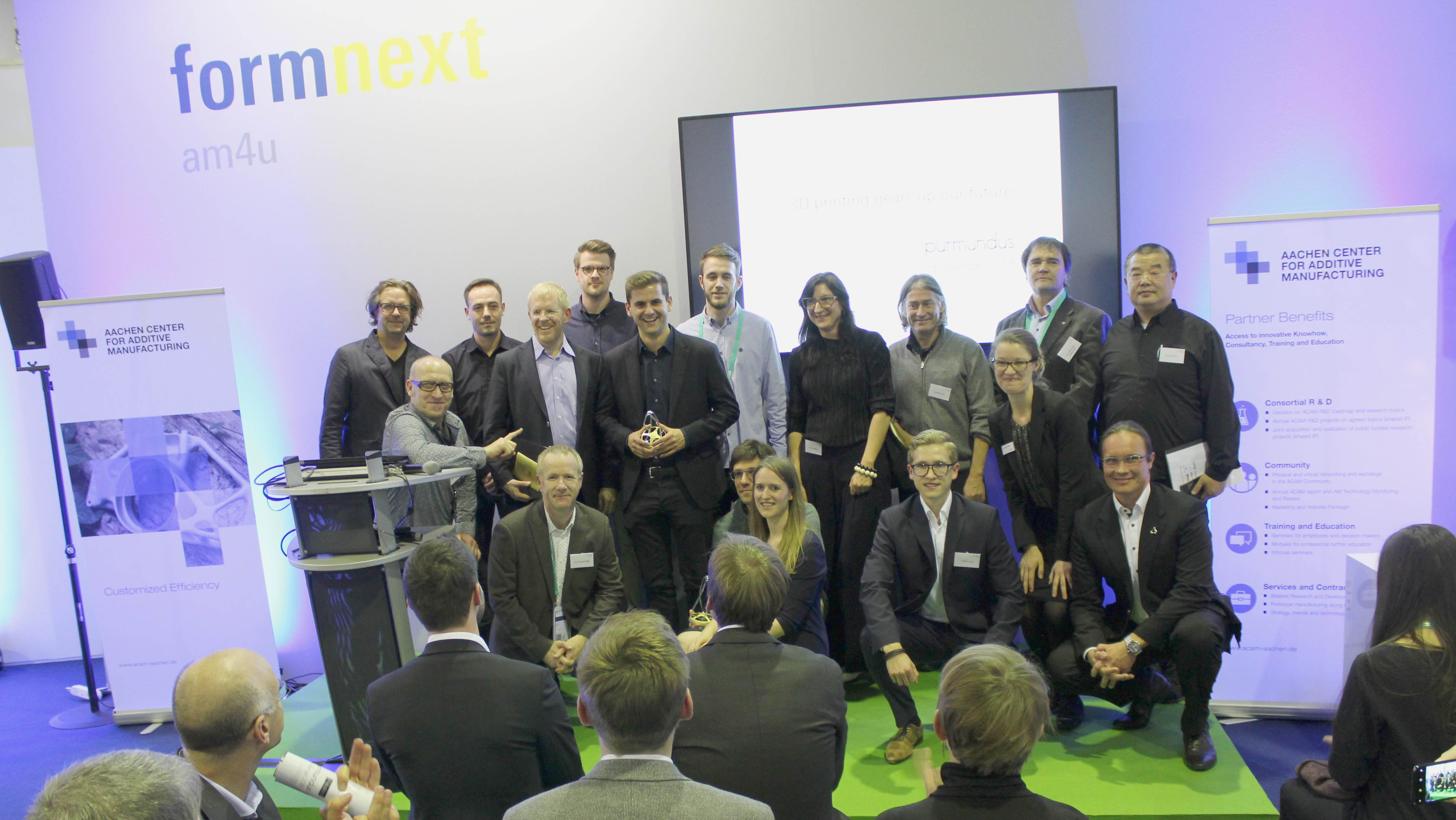
Las soluciones que se premiaron demuestran que tanto la industria, como las universidades, los estudios de diseño y las empresas de nueva creación están bien encaminados para conformar nuestro futuro de manera sostenible y positiva con la impresión 3D. “La impresión 3D ha dejado de ser una moda para estar en sintonía con el resto” afirma Corinna Ray, directora del purmundus challenge. A lo que Christoph Behling, fundador de Christoph Behling Design Ltd. y miembreo del jurado purmundus challenge, añade: “El purmundus challenge demuestra que la impresión 3D consigue cambiar cualquier topologia existente desde hace décadas o siglos; y es capaz de crear formas completamente nuevas con funciones totalmente distintas”.
Bajo el lema “la impresión 3D nos prepara para el futuro” 34 finalistas de todo el mundo presentaron sus extraordinarias creaciones del 13 al 16 de noviembre en la Feria Formnext. Proporcionaron perspectivas interesantes e ideas sobre cómo se podrán diseñar los productos en el futuro y sobre el papel que va a jugar en ello la impresión 3D.
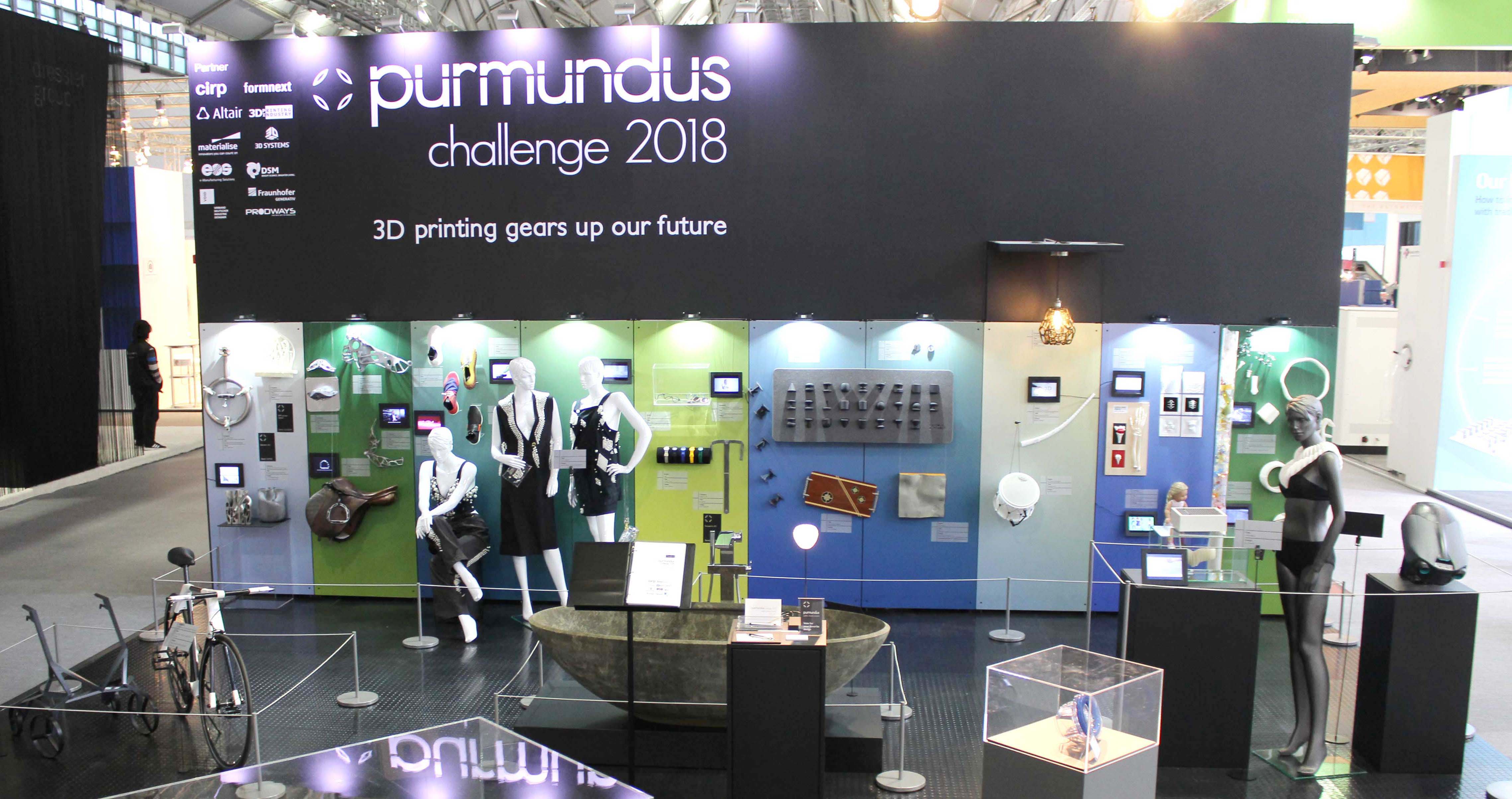
Los ganadores de este año son:
1. Premio: Keyed wind instrument
3D Music Instruments I Ricardo Simian

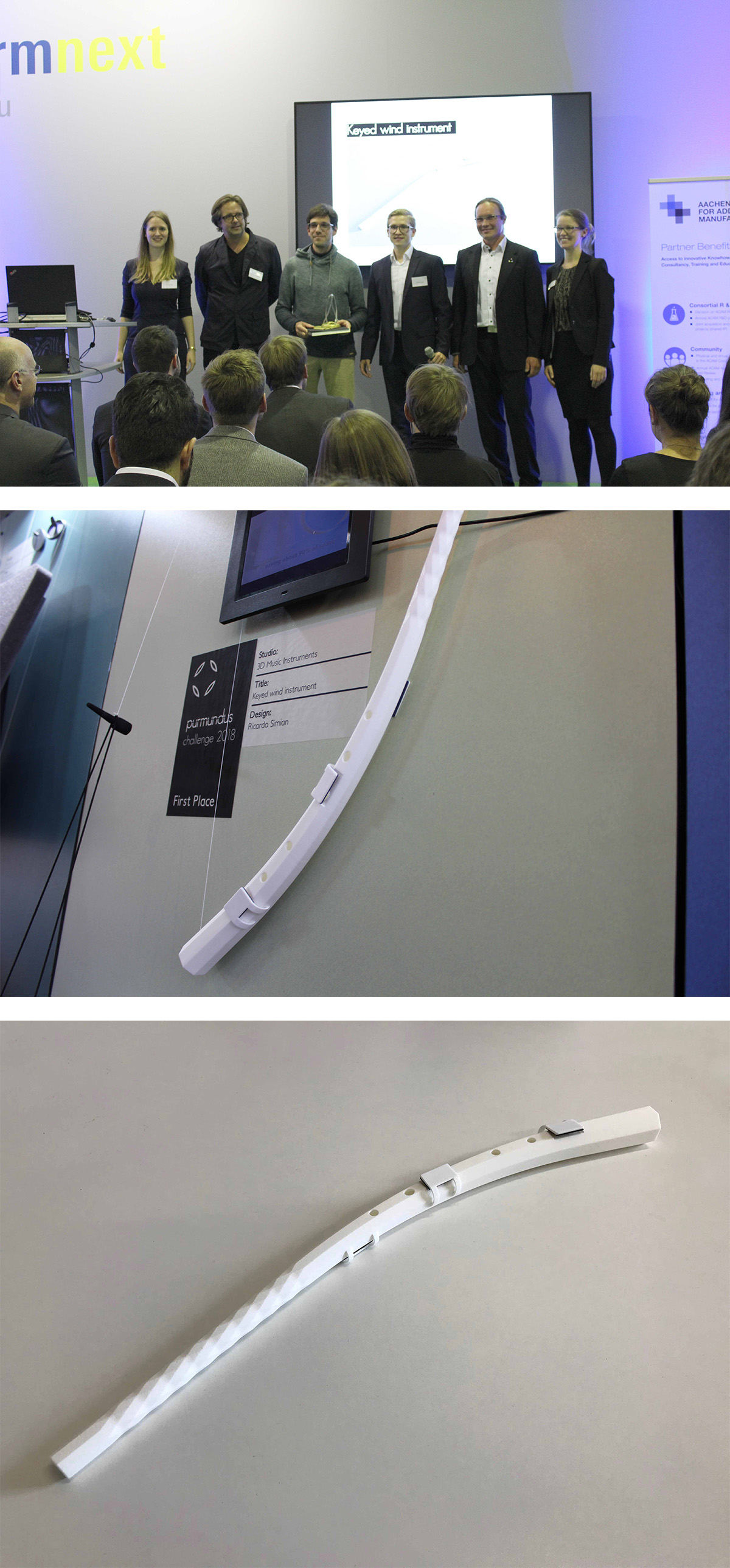
Las primeras llaves de las que existe evidencia documentada, que se usaron para extender el alcance natural de los dedos y poder así tapar los agujeros, se crearon para las notas graves de la bombarda, un instrumento con doble lengüeta de la baja Edad Media. Desde entonces, los fabricantes de instrumentos han aplicado el mismo concepto para la fabricación de los saxofones, clarinetes y oboes modernos, en los cuales los dedos no interactuan directamente con los agujeros y estos se pueden alcanzar gracias a un sistema de teclas complejo que se reparte a lo largo de instrumentos que llegan a alcanzan hasta los dos metros de longitud.
Sin embargo, el principio fundamental de este concepto de teclas no ha variado desde sus inicios, un mecanismo externo que se añade al instrumento para descubrir los agujeros y que se activa pulsando unas llaves. Las versiones modernas de estos instrumentos producidos en masa se rigen en función de este principio, lo que significa que son las teclas y no el cuerpo del instrumento en sí las que generan la mayor parte de los costes de producción de los mismos.
Esta nueva perspectiva de diseño de llaves consiste en integrar las llaves al instrumento y aprovechar las caracteristicas de flexibilidad de los materiales para la impresión 3D con tecnología SLS para permitir la producción de llaves funcionales sin ningún tipo de mecanismo adicional o muelles. Se pueden incorporar las llaves a la impresión de este tipo de instrumentos si se realiza un diseño cuidadoso de los mismos.
He elegido la corneta para ejemplificar este proceso. Se trata de un instrumento de viento del Renacimiento que desapareció muy pronto de la escena musical y que se siguió desarrollando mediante la adición de llaves.
Hoy en día, los músicos que tocan la corneta tienen que luchar con la longitud del instrumento y con la distribución inusual de los agujeros para poder tocar. Con la adición de este tipo de llaves conseguimos que la corneta sea, por primera vez en la historia, más ergonómica. Las almohadillas de silicona situadas debajo de las llaves son los únicos elementos no impresos con tecnología 3D que se necesitan añadir a este diseño en el proceso de post-producción.
Este concepto no se limita únicamente a este instrumento, si no que su desarrollo se puede adaptar a otro tipo de instrumentos de viento.
Escuche la melodía de este instrumento Keyed wind instrument http://cornetti.3dmusicinstruments.com/cornetti/
2. Premio: Adidas Grit
Aarish Netarwala

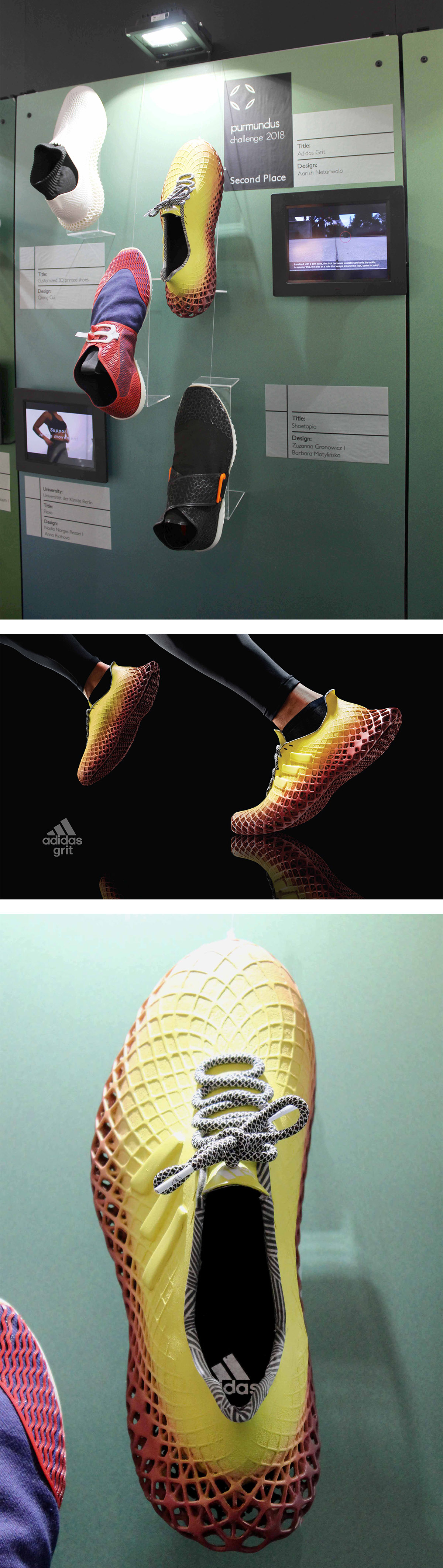
El concepto de las Grit está basado en investigaciones sobre el el entrenamiento de resistencia en dunas de arena. Algunos de los mejores atletas del mundo, como Kobe Bryant, Kevin Durant y otros atletas de élite, entrenan en arena para aumentar el nivel de dificultad de los ejercicios. El entreanmiento en arena ralentiza los movimientos de manera considerable y les permite entrenar los movimientos explosivos de los músculos y fortalecer determinados músculos para favorecer la aceleración. El objetivo es que al correr con las Grit se tenga la misma sensación que al correr por la arena. El pie está recogido en una estructura reticular. Cuando el pie golpea el suelo, la estructura reticular se colapsa y disipa la energía del impacto. Esta es una sensación muy agradable para las articulaciones, ya que la zapatilla absorve gran parte del impacto.
Cuando el atleta transfiere una parte del peso corporal a la parte delantera del pie, la estructura de la suela está diseñada para hundirse, oponiéndose al movimiento de avance del atleta. Cuando se eleva el pie del suelo, la suela reticular vuelve a su estado original y está preparada para el siguiente impacto.
El objetivo es aumentar la cantidad de energía necesaria para el entrenamiento usando el modelo Grit en cualquier superficie. Esta experiencia ofrece a los atletas un entrenamiento más intenso y efectivo en un menor periodo de tiempo.
Estos fueron los objetivos de diseño del modelo Grit:
- Crear un zapato de entrenamiento de resistencia para que los atletas pudieran entrenar en cualqueir superficie replicando las propiedades de la arena y todo ello aunado en un único diseño.
- Crear un diseño que fuera capaz de disipar la energía cuando el pie impacta en el suelo y así conseguir que los músculos de las piernas de los atletas se cansen antes. Este es un concepto contrario al que ofrecen las zapatillas de entrenamiento disponibles en el mercado hoy en día, que devuelven la energía al usuario y hacen el entrenamiento más fácil.
- Crear un diseño que haga posible aumentar la resistencia y contribuir a que los atletas alcancen rápidamente sus propios límites y puedan mejorarlos.
- Crear un diseño de zapatilla que personifique la mentalidad de un atleta que busca constantemente superar sus propios límites.
Al trabajar con distintos tipos de materiales me di cuenta de las ventajas que ofrece usar estructuras reticulares en los zapatos; y no precisamente por las razones por las que se usan hoy en día para aumentar el rendimiento o devolver la energía. En realidad creo que las estructuras reticulares son buenas para consumir energía. Al realizar la impresión de distintas estructuras reticulares aprendí para qué eran buenas sus propiedades físicas, y entonces desarrollé un prototipo para ir probando con distintas partes del pie y con distintas estructuras. Mientras que el talón recibía la mayor parte del peso y del impacto, la parte delantera del pie se hundía suavemente para contrarestar la ejecución del movimiento, como pasa con la arena. Y esto es lo que condujo a desarrollar el resultado final de Grit.
Grit es un modelo único por los siguientes motivos:
1 Ningún calzado disponible en el mercado actual se adecúa a las necesidades ni tampoco ofrece las ventajas del entrenamiento de resistencia. Grit es el primer modelo de este tipo y consigue crear una nueva categoría de calzado de entrenamiento que se ajusta a las necesidades corporales de los deportistas de hoy en día.
2 Grit dificulta el entrenamiento de los atletas en vez de hacerlo más sencillo. Este es un concepto nuevo para el calzado, ya que el diseño tradicional se centra en ofrecer a los atletas todas las facilidades posibles.
3 La estructura del modelo Grit es única, ya que la suela rodea al pie. Básicamente, el pie está envuelto por completo por una suela blanda que lo soporta y que absorve el impacto en cualquier ángulo como pasa con la arena.
4 El modelo consta de dos partes principales para el proceso de producción y montaje. Un calcetín de tela se introduce en una suela reticular de poliuretano elastomérico (EPU) reciclable e impreso con tecnología 3D. Ambas partes están entretejidas. Los materiales son fáciles de separar y de reciclar después de su uso. Las suelas tradicionales están hechas con goma EVA y en el proceso de producción se usan adhesivos fuertes para unirlas que hacen imposible que posteriormente los zapatos se puedan reciclar.
5 La estética visual del modelo Grit desafía los límites de lo que es posible conseguir usando materiales y técnicas de producción emergentes.
Las ventajas que Grit ofrece a los clientes – Adidas.
1 Grit se basa en una adaptación personalizada usando los datos biométricos de cada cliente. Esto crea un canal de venta directo al consumidor que elimina la necesidad de intermediarios y aumenta considerablemente el margen de beneficio por cada par de zapatillas.
2 Grit no necesita ningún tipo de molde para la suela. Generalmente, el coste de la suela externa del calzado asciende a varios miles de dólares por cada molde. El proceso de producción de Grit elimina la necesidad de crear moldes de más de veinte tallas distintas. Esto evita que se hagan altos costes de inversión reduciendo así los riesgos.
3 Aprovechando la futura plataforma de impresión 3D de Adidas, el canal para la producción del modelo Grit ya está disponible y ofrece a Adidas la posibilidad de hacer una inversión de bajo riesgo. Cada par se puede confeccionar después de haber solicitado el pedido, se elimina la necesidad de tener existencias y el pago se produce antes de que se produzcan las zapatillas.
4 La innovación juega un rol fundamental en la imagen de las marcas de calzado de deporte, que genera entusiasmo entre los usuarios amantes del calzado. Esta línea de productos innovadores contribuye al reconocimiento de Adidas y consigue establecer una tendencia que impulsa el futuro del calzado.
Grit pone a disposición de deportistas de todo el mundo el entrenamiento en arena y la experiencia del estilo de vida. Con la suela de Grit, que absorve la mayor parte del impacto, los huesos y las articulaciones del cuerpo se sobrecargan menos, consiguiendo que deportistas de mayor edad también entrenen en superficies duras como el asfalto.
En resumen podemos decir que Grit abre un abanico de oportunidades aún por explotar en la escena deportiva y aumenta los límites de funcionamiento y producción del calzado.
Vídeos:
https://www.youtube.com/watch?v=yTt0kc1ZthM
https://www.youtube.com/watch?v=YvUSMoZYS_E
3. Premio: Bionisch inspirierter Kombibrenner
Siemens AG, Corporate Technology I Dr. Christoph Kiener I Manuel Biedermann

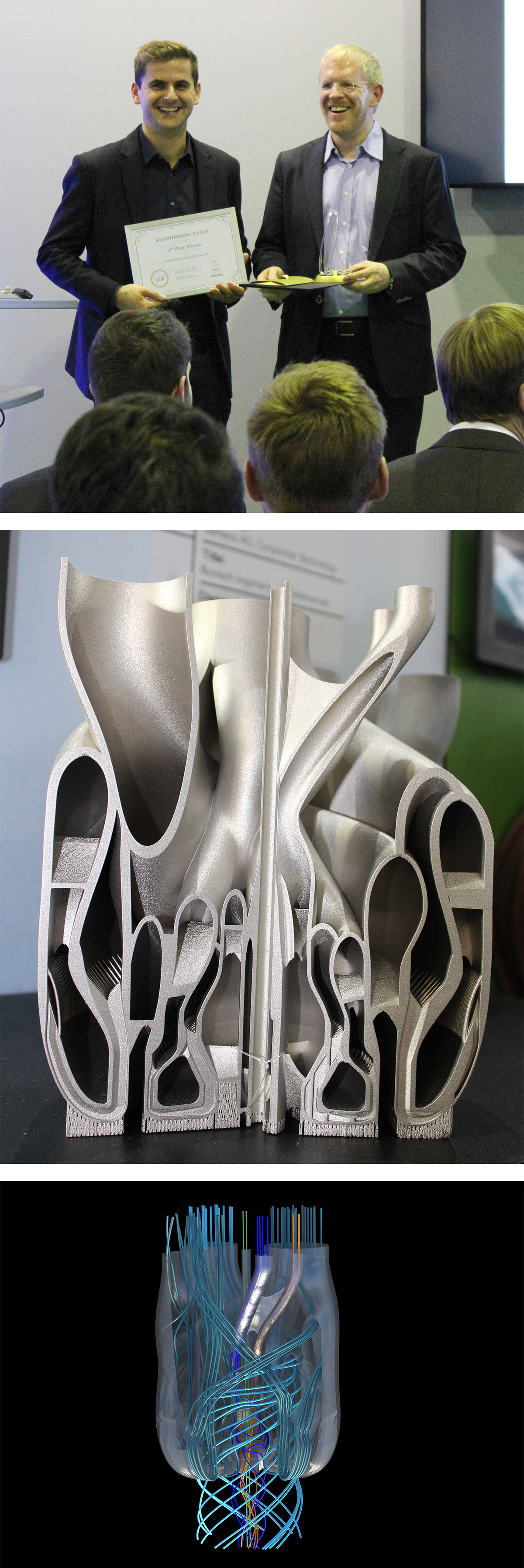
1. Las estructuras finas de 1 mm ofrecen una refrigeración óptima en las pareces frontales calientes y tienen un alto grado de resistencia
2. Los distribuidores de líquido optimizados dirigen el líquido refrigerante y los reactivos con una mínima resistencia de flujo.
3. Las conexiones tubulares permiten un montaje fácil de todo el sistema y ahorran tiempo.
4. Estos tres aspectos están unidos en una única pieza diseñada con las reglas de diseño de la fabricación adititva sin ningún tipo de estruturas internas de soporte.
El proceso de dieseño funcional toma como ejemplo la naturaleza y utiliza algoritmos evolucionarios asistidos por software. La distribución uniforme y eficiente del líquido refrigerante y de los reactivos para la aplicación a altas temperaturas se optimiza realizando un gran número de simulaciones. En comparación con las construcciones convencionales, este diseño hace posible un uso más eficiente de los recursos, un proceso de fabricación más flexible y simple, así como una mayor vida útil de sus componentes. Los contenidos de este estudio preliminar son pioneros para las futuras aplicaciones de los métodos de fabricación generativa para la producción de componentes para la industria de transformación.
Un experimento que ejemplifica la efficiencia de la refrigeración:
A pesar de las condiciones que calientan la pieza convencional a 600 °C y que pueden tener como consecuencia que se produzcan grietas por la tensión, la fina pared frontal de tan solo un milímetro con canales está refrigerada y mantiene constante la estabilidad mecánica y la resistencia a la compresión. La llama del soplete solo calienta el objeto de prueba – para este experimento se trata del anillo exterior que se ha producido por separado –hasta los 180 °C cuando fluye el refrigerante, hecho que ha sido verificado usando cálculos teoréticos de dinámica de fluidos computacional (CFD). Si se separa la fuente de calor, la superficie de la pieza se refrigera por completo en menos de un segundo, lo que permite incluso tocarla y hace que sea menos susceptible a agrietarse cuando se somenten fuerzas alternantes.
El gran número de canales pequeños que contiene la estructura la hacen altamente resistente a la compresión. Con una presión de ensayo experimental de 56 bares necesaria para la certificación TÜV, la pieza se mantuvo intacta a pesar de experimentar una presión interior de 240 bares.
Ya se han realizado pruebas experimentales con más de 5000 horas de servicio con una temperatura de cocción de 1500 °C en instalaciones de combustión industriales con una potencia térmica de 200 MW con una de las piezas con la certificación TÜV conforme a la directiva sobre equipos de presión.
Mención especial: "Mit 4D-Druck zur Bewegung"
Dorothea Lang

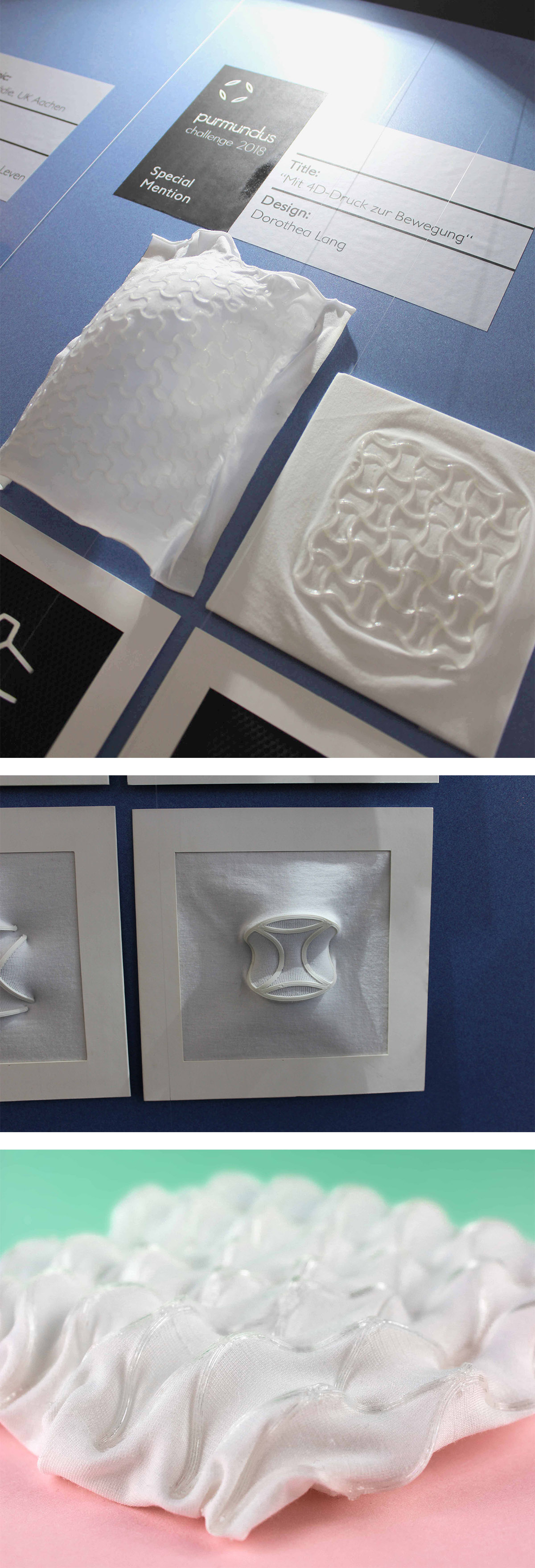
El trabajo de fin de máster “Impresión 4D para el movimiento“ se centró en desarrollar tejidos dinámicos, inteligentes y con forma cambiante. El objetivo era retomar la idea de la impresión 4D para crear tejidos funcionales, adaptables y con propiedades activas. Se llevaron a cabo un gran número de estudios con material experimental usando la impresión 3D para investigar la manera de conseguir acabados en tejidos con una impronta 3D para generar un movimiento determinado.
Esta idea se pudo llevar a cabo gracias a la combinación específica de determinada tensión en el tejido y su correspondiente estructura 3D, así como usando un filamento de impresión “inteligente“ que puede recordar su forma. Esta combinación de materiales hace posible que toda la superfice del tejido tenga memoria de forma y la inteligencia material del material que se imprime, lo que permite especificar con precisión el patrón de movimento que funciona de manera independiente en respuesta a determinados cambios de temperatura. El diseño geométrico que se crea se imprime dotándolo de una forma permanente. Cuando aumenta la temperatura cambia la estructura del plástico. Lo que empieza como un obejto sólido se convierte en un material suave y flexible que adquiere una forma nueva. Esta forma temporal se endurece rápidamente convirtiéndose de nuevo en un objeto sólido. Si de nuevo aumenta la temperatura, se activa la memoria material del polímero que hace que todo el tejido retome la forma permanente inicial con la que fue impreso en un principio.
La ortopedia es un ámbito de aplicación muy interesante para este tipo de tejidos, y por ello se produjo la elaboración de los mismos en cooperación con la empresa Otto Bock HealthCare GmbH. Un amplio número de estudios de materiales sirvieron como base para la elaboración de dos conceptos que corroboraron cómo se podría usar la fabricación aditiva en un futuro para producir vendajes adaptables e invidualizados.
Concepto: „Vendaje dinámico“
El primer enfoque conceptual se basa en la idea de un método sencillo y rápido para crear vendajes personalizados. El procedimiento, que conlleva la impresión 3D de estructuras que se han creado a medida de cada paciente en tejidos que se producen con métodos convencionales, permite aportar al vendaje una forma ajustable y también aplicar directamente elementos aislados de refuerzo. Es posible imaginar que en un futuro se puedan fabricar los vendajes por órden de los especialistas en ortopedia. Esto conllevaría crear datos 3D escaneados de determinadas partes del cuerpo del paciente usando aplicaciones los conviertan en un archivo de impresión específico para cada cliente para después simplemente imprimirlo sobre el tejido previamente tensado o sobre el vendaje. De esta forma se genera un vendaje que se adapta perfectamente a la anatomía de cada paciente y asegura la estabilidad de la posición fomentando el movimiento de la articulación correspondiente.
Concepto: „El vendaje inteligente“
La capacidad de adaptarse al cuerpo del paciente es una propiedad muy importante que tienen que tener los vendajes para ofrecer cierto grado de comfort y contribuir al proceso de rehabilitación. Al igual que en el concepto anterior, la impresión 3D en tejidos parte del vendaje como base, si bien al contrario que en el caso del “vendaje dinámico“, la individualización se produce después del proceso de producción. De esta manera sería posible tener vendajes almacenados y adaptarlos a las necesidades de cada paciente si fuera necesario. Esta habilidad para adaptar con posterioridad los “vendajes inteligentes“ se consigue usando en la impresión un filamento inteligente con memoria de forma.
Con este principio sería posible transferir el comportamiento inteligente del material de impresión a todo el vendaje gracias a la aplicación de una estructura de polímero con memoria de forma. De esta manera el vendaje inteligente se puede adaptar facilmente a todo tipo de geometrías corporales aumentando la sujección. La función de memoria de forma en el plástico impreso permitiría, en teoría, reajustar el vendaje una y otra vez en respuesta de las nuevas necesidades o del progreso del cuadro clínico. La habilidad para usar el vendaje inteligente de manera continuada podría suponer una ventaja en comparación con los vendajes convencionales.
Premio de Innovación: Fungus-like additive materials
Singapore University of Technology and Design I Javier G. Fernandez I Stylianos Dritsas

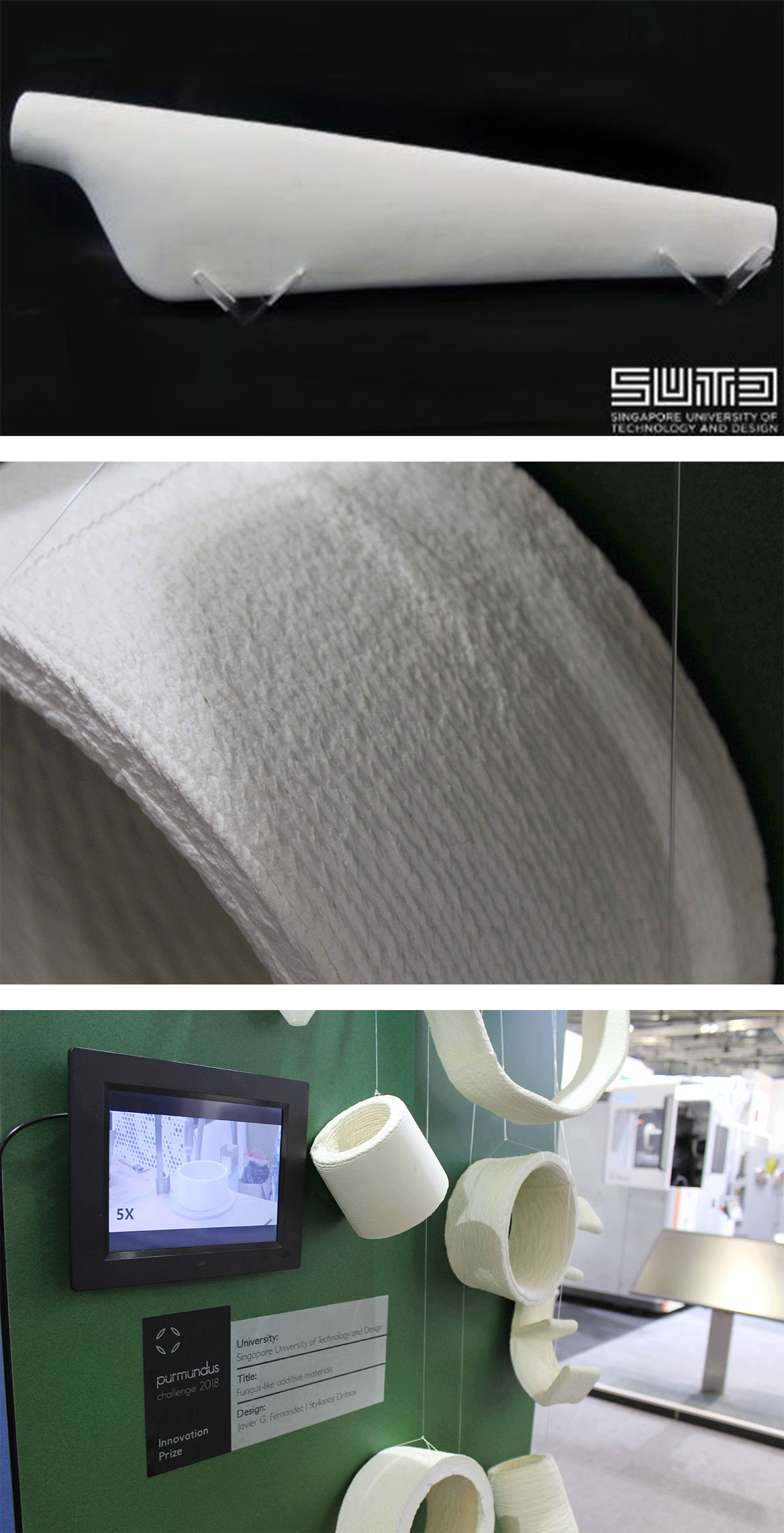
La celulosa es uno de los los componentes orgánicos más abundantes y extendidos en la tierra, y además es un subproducto industrial. Sin embargo, a pesar de que se han realizado muchos estudios durante décadas, el uso ascendente de la celulosa para fabricar objetos 3D aún está repleto de problemas que restringen sus aplicaciones prácticas: derivados con enormes efectos contaminates, su uso en combinación con plásticos, la falta de escalabilidad y el alto coste de producción.
Sin embargo, investigadores de la Universidad de Tecnología y Diseño de Singapur (SUTD) han podido probar recientemente la aplicación de celulosa para la manufactura y producción de objetos 3D de gran tamaño. El enfoque que plantean diverge de la asociación común de celulosa con plantas verdes y está inspirada en la pared de los hongos oomicetos que se reproduce introduciendo cantidades pequeñas de quitina entre las fibras de celulosa. Los materiales adhesivos resultantes similares a los hongos (FLAM) son resistentes, ligeros y económicos; además de que se pueden moldear y procesar usando técnicas de ebanistería.
Este material es completamente sostenible ecológicamente ya que no se utiliza ningún tipo de disolvente orgánico o plástico sintético para su elaboración. Se puede escalar y reproducir en cualquier lugar sin tener que disponer de ninguna instalación especial. FLAM es a su vez biodegradable al cien por cien en condiciones naturales y en el exterior en plantas de compostaje. El coste de FLAM se encuentra dentro de los márgenes de los plásticos comunes y es diez veces menor que el coste de los filamentos estándar para la impresión 3D, como por ejemplo el PLA (ácido poliláctico) y el ABS (Acrilonitrilo-butadieno-estireno); lo que lo convierten no solo en más sostenible si no a su vez en un sustituto más rentable. Los investigadores han seguido desarrollando una técnica de fabricación aditiva específica para este material.
El codirector de esta investigación, Javier Gómez Fernández, profesor adjunto en la SUTD, y también conocido por haber desarrollado Shrilk dijo: “creemos que este primer proceso de fabricación aditiva a gran escala con los polímeors biológicos de mayor presencia en la tierra será el catalizador para la transición hacia los modelos de fabricación circular y respetuosos con el medio ambiente, donde los materiales se producen, se usan y se degradan en sistemas regionales cerrados. Esta reproducción y fabricación con la composición de materiales encontrada en las paredes de los hongos oomicetos, es decir celulosa virgen, pequeñas cantidades de chitosan ‘la segunda molécula orgánica más abundante en la tierra’ y baja concentración de ácido acetico, es probablemente uno de los logros tecnológicos con más éxito en el sector de los materiales inspirados en la naturaleza.“
El codirector y profesor adjunto en la SUTD Stylianos Dritsas añade: “creemos que los resultados que aportamos suponen un punto de inflexión para la fabricación global con un impacto más amplio en distintas áreas que abarcan desde la ciencia de materiales, a la ingeniería medioambiental, la automatización o la economía. Hasta ahora nos hemos centrado en desarrollar la tecnología fundamental, pero se ha invertido poco tiempo en lograr aplicaciones específicas. Ahora nos encontramos en la fase de buscar colaboradores en la industria que quieran acercar al mundo esta tecnología desde el laboratorio“.
Con el aumento de los resíduos y de la contaminación está creciendo la necesidad de crear procesos de fabricación más sostenibles. Establecer una tecnología basada en polímeros compostables no modificados disponibles en abundancia y que no requiera campos de cultivo o recursos forestales promoverá la transición hacia una producción respetuosa con el medio ambiente y a una sociedad sostenible.
Basándonos en los principios de Shrilk, hemos desarrollado la fabricacion aditiva con dos de los polímeros orgánicos de mayor abundancia en la tierra. Los materiales aditivos similares a los hongos permiten la impresión 3D en cualquier ecosistema del mundo sin tener la necesidad de transportar material, y es precisamente la pieza que faltaba para el desarrollo global de modelos de fabricacon circular basados en la fabricación aditiva. Este hecho se ha demostrado con la producción de distitos objetos, el último de ellos una hélice de turbina de 1.2 metros creada con fabricación aditiva. El material de la hélice tiene un coste similar a los plásticos comunes y es veinte veces más barata que los filamentos de impresión estándares (PLA, PETG, ABS...), pero lo que es más importante, es que se produce en su totalidad con componentes naturales, sin modificaciones, y permite la producción y degradación se integren perfectamente con los ciclos ecológicos.
Vídeos:
https://www.youtube.com/watch?v=V8B1Q_1M5UY&index=3&list=PL4vr85uZfzzljeWm4ag3QjQsDojqL4Xrw&t=0s
https://www.youtube.com/watch?v=fd2Q5KvRVOs&index=5&list=PL4vr85uZfzzljeWm4ag3QjQsDojqL4Xrw&t=0s
https://www.youtube.com/watch?v=Zk0fVNDZDug&index=4&list=PL4vr85uZfzzljeWm4ag3QjQsDojqL4Xrw&t=0s
https://www.youtube.com/watch?v=ThOksDvlGD4&index=2&list=PL4vr85uZfzzljeWm4ag3QjQsDojqL4Xrw&t=0s
Premio del público: Die erste Badewanne der Welt aus dem 3D Drucker
Sandhelden GmbH & Co. KG I Sebastian Hermann
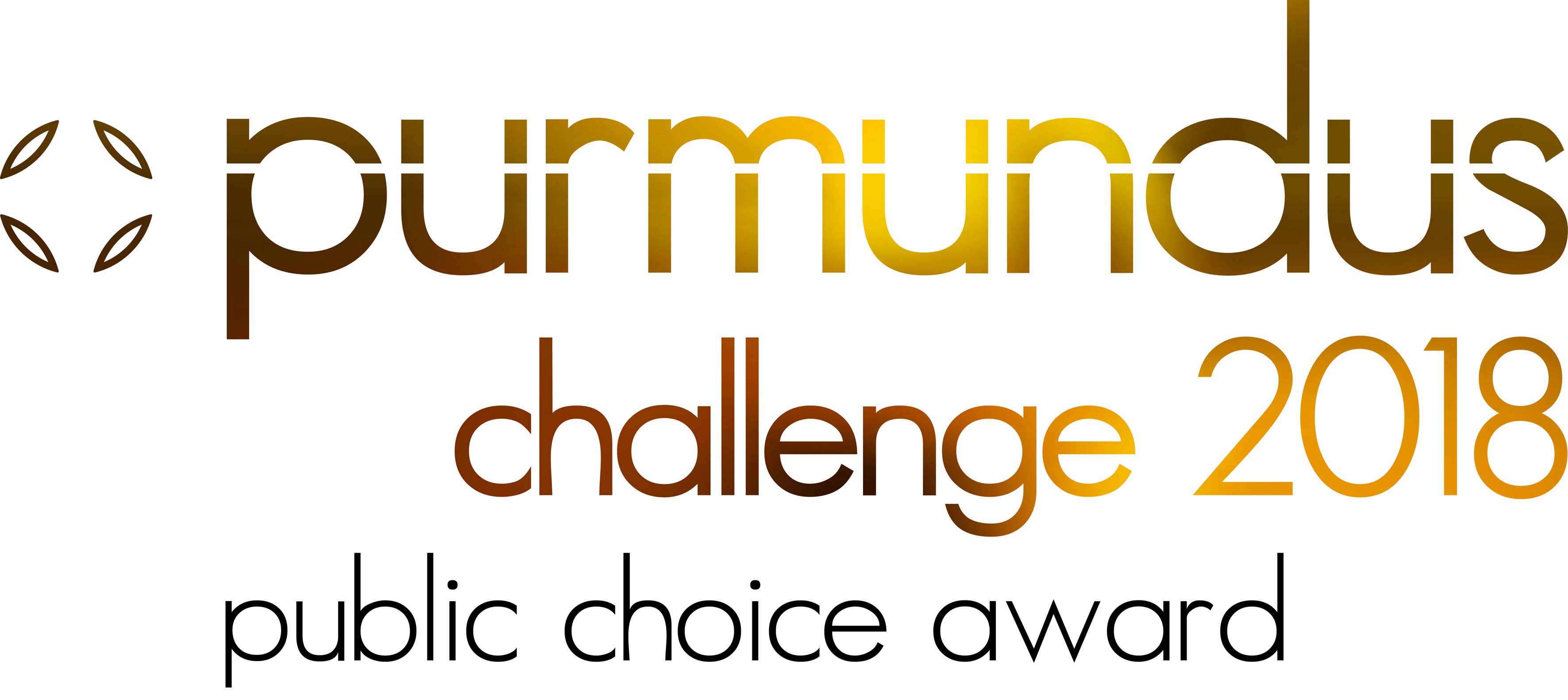
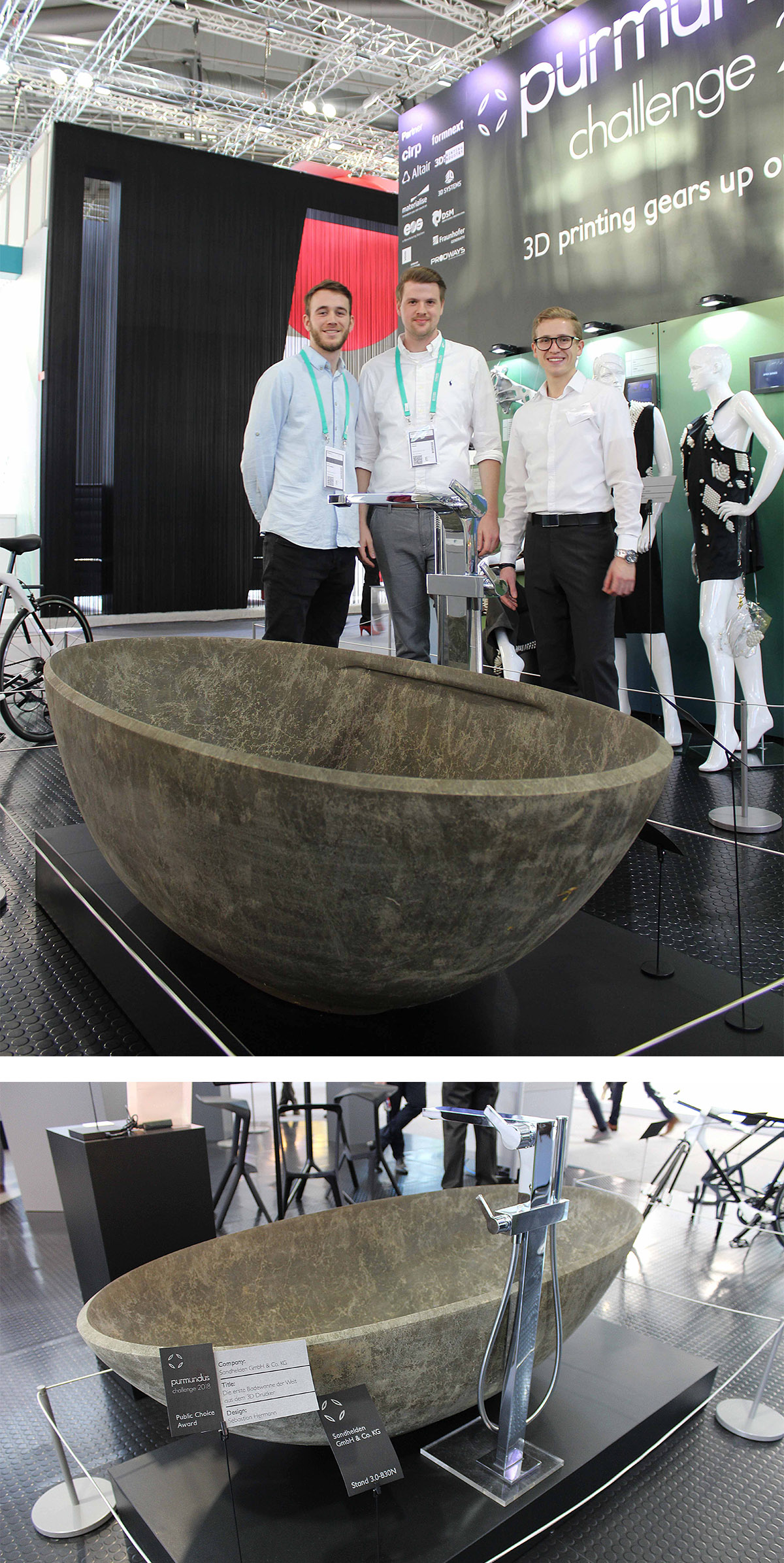
Gracias a la tecnología que usamos, somos capaces de crear la primera bañera impresa con arena en una sola pieza. Ayudándonos de las técnicas de procesado posterior conseguimos dotarla con las características técnicas propias que requieren este tipo de productos.
La textura que aporta este tipo de material a la bañera hace que sea una pieza única de diseño desconocida hasta ahora.
Vídeo: https://www.youtube.com/watch?v=0P4rQw-D1d0
Estos son los finalistas de este año:
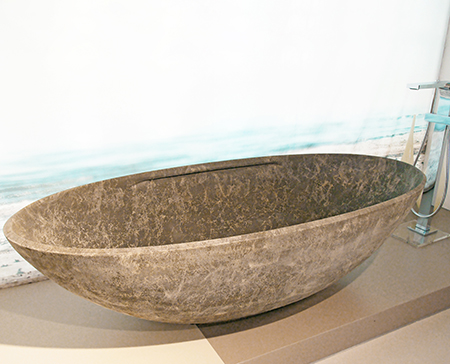
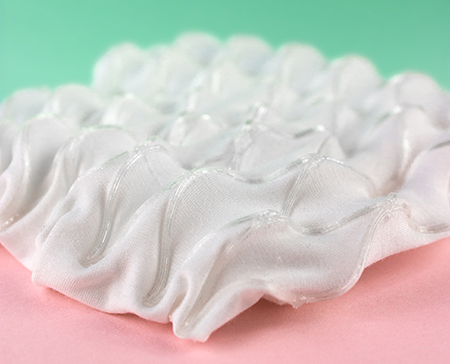
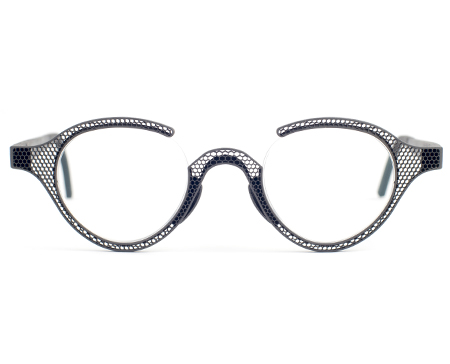
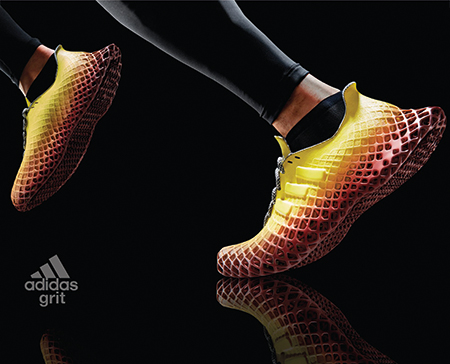
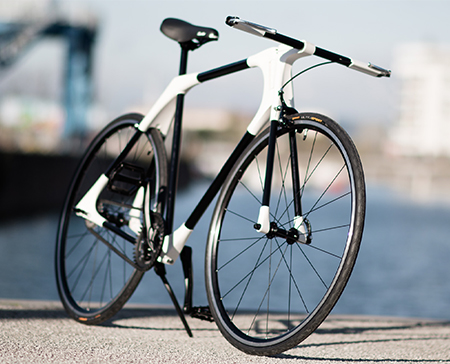
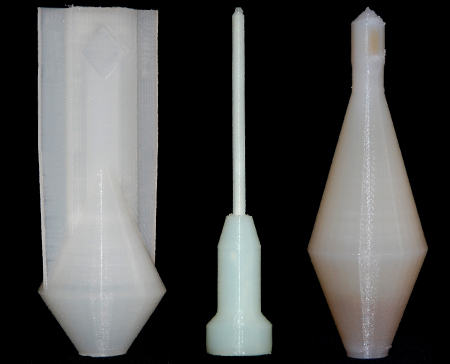
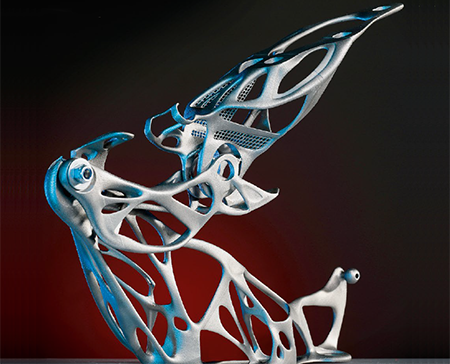
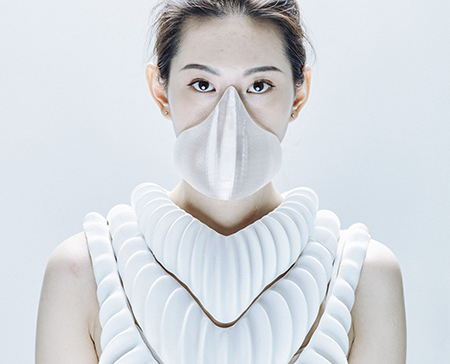
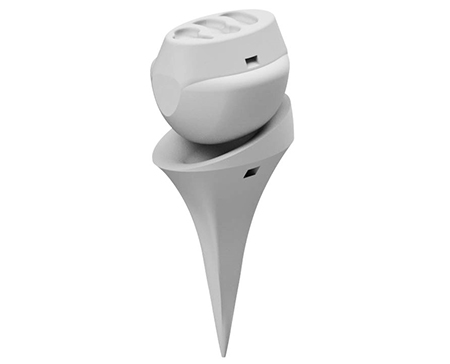
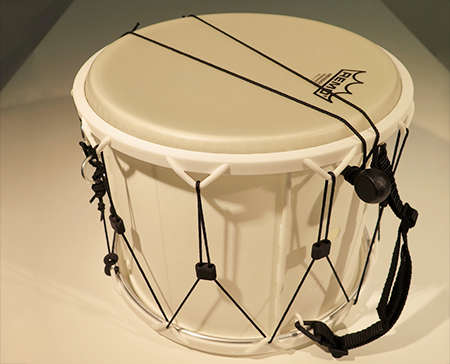
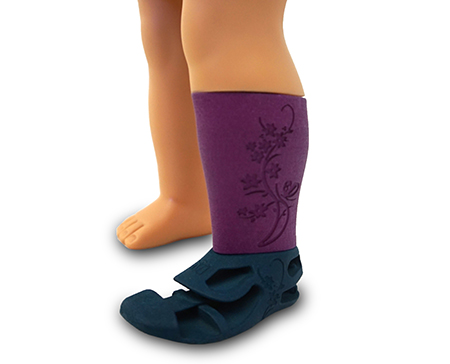
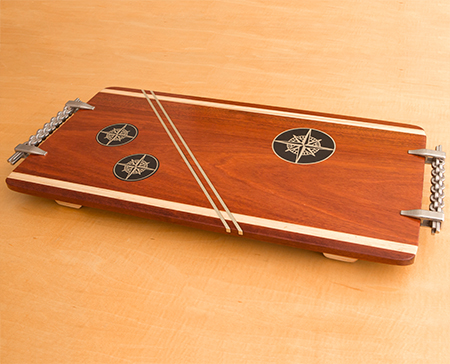
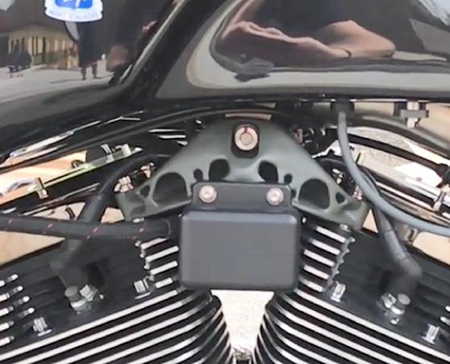
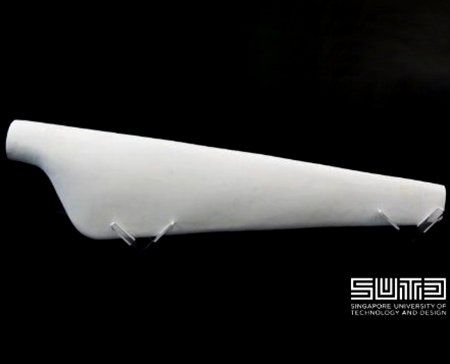
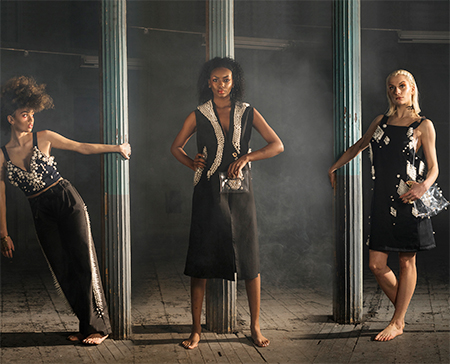
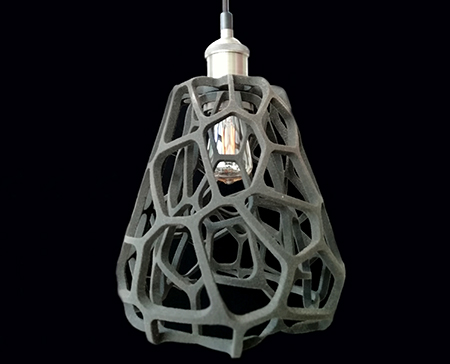

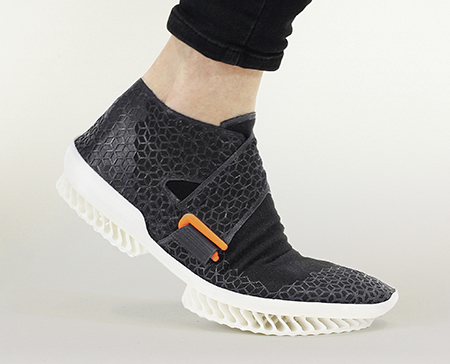
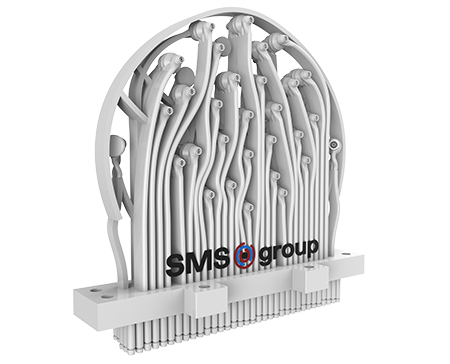
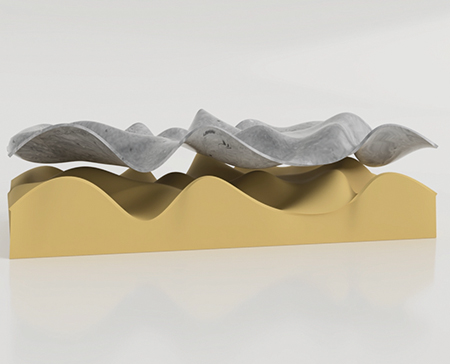
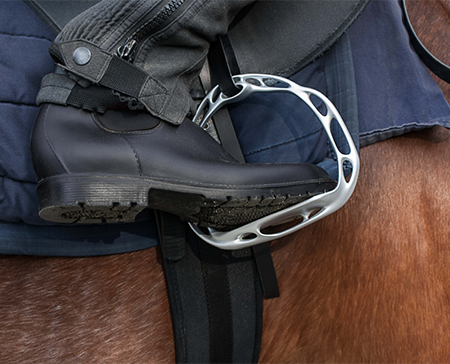
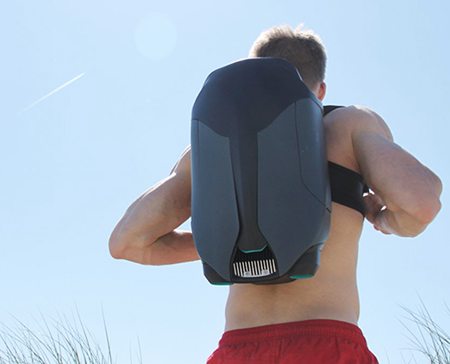
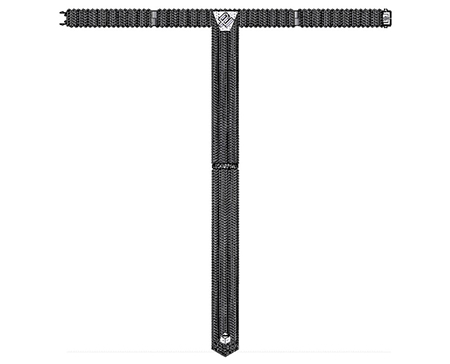
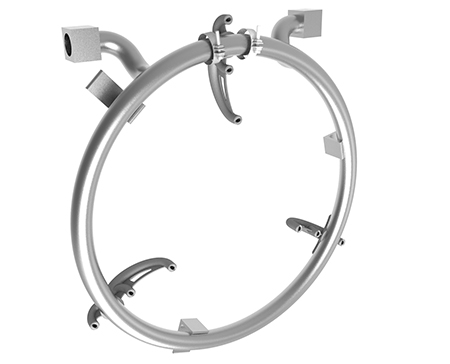
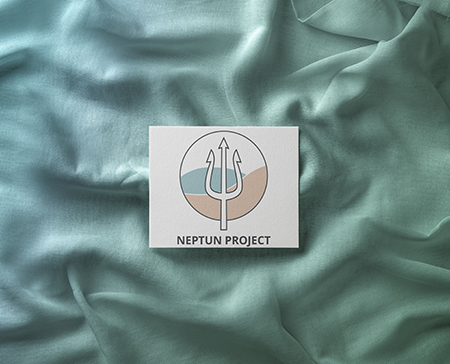
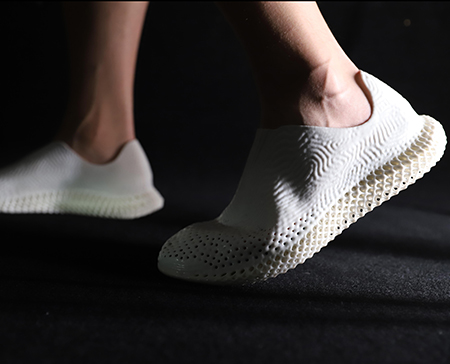

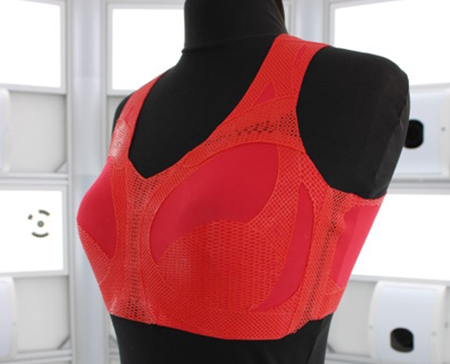
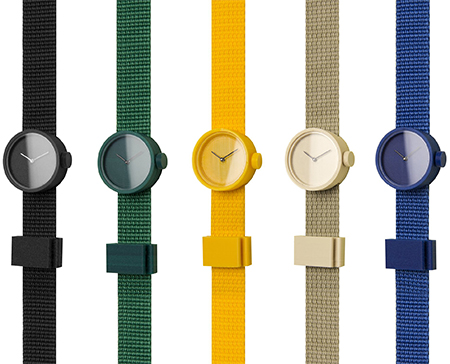
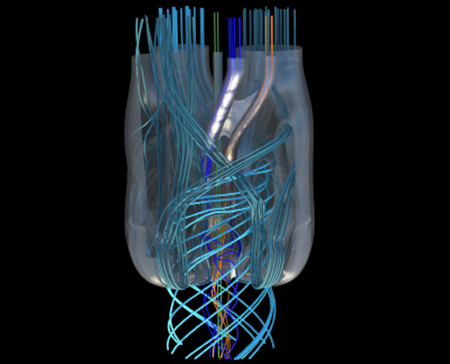
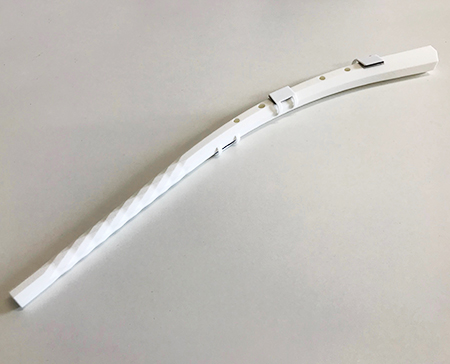
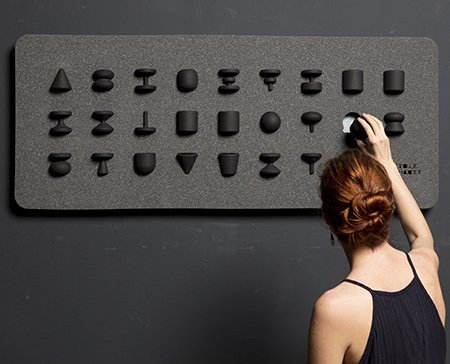
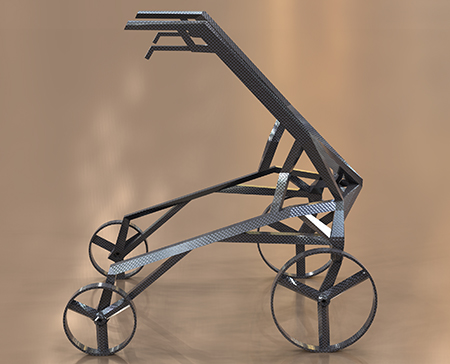
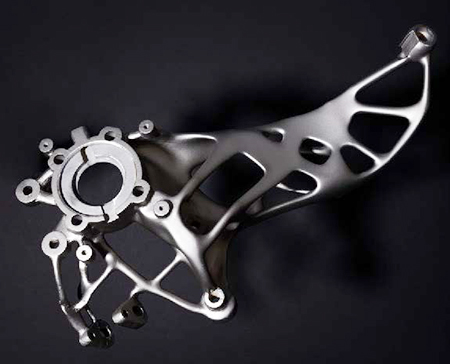
×
Handout Finalists: Los finalistas de la purmundus challenge 2018 [pdf: 4,1 MB]
!Desde aquí nos gustaría dar las gracias al jurado y a los colaboradores!
Jurado 2018
Christoph Behling - Christoph Behling Design Ltd.Prof. Richard Bibb - Loughborough University
Isabelle Fröhlich - Volkswagen AG Tilla Goldberg - Ippolito Fleitz Group GmbH Dr. Alexander Hildebrandt - Festo AG & Co. KG Frank Kleemann - Diseñador industrial autónomo Andreas Pany - Ernst Strassacker GmbH & Co. KG Prof. Dali Sun - Beijing Institute of Technology Graham Tromans - G. P. Tromans Associates Rainer Zimmermann - zimmermann produktgestaltung